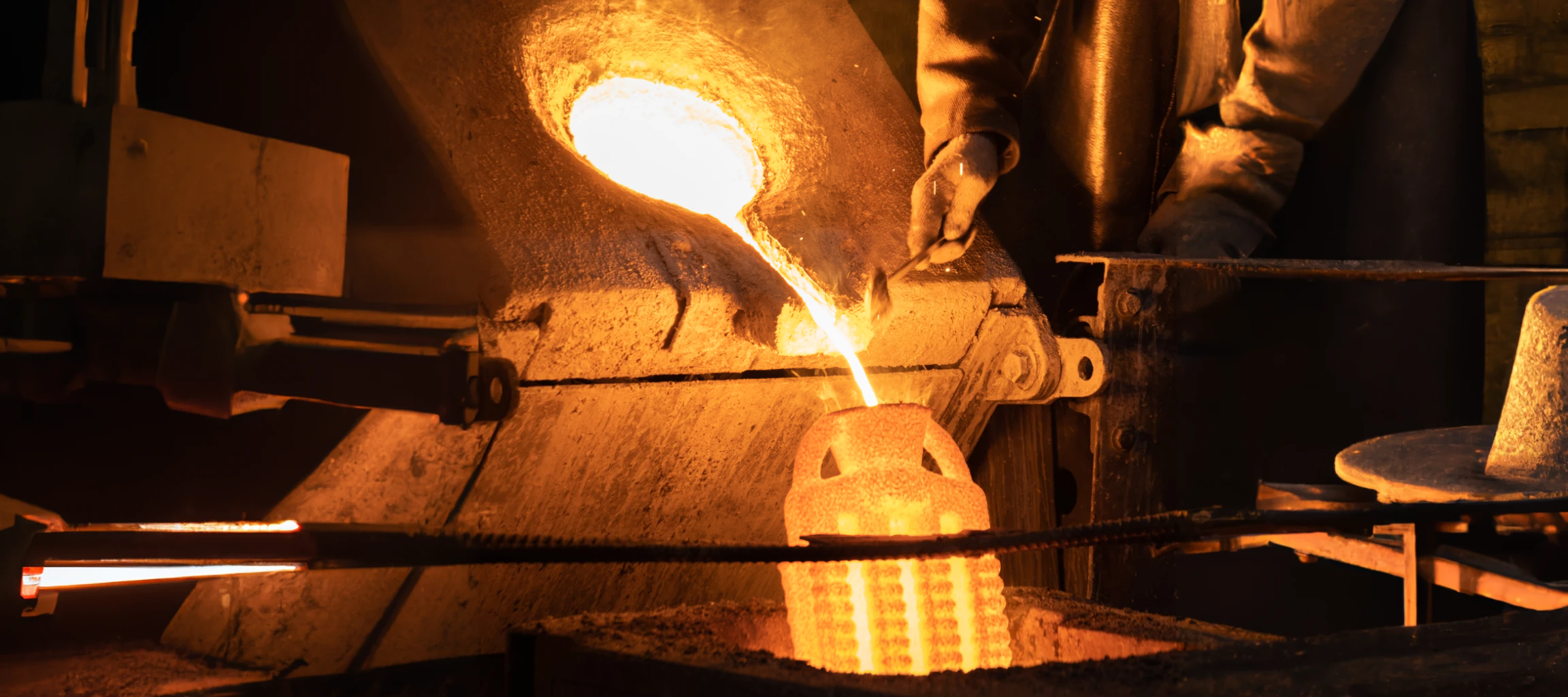
Feinguss
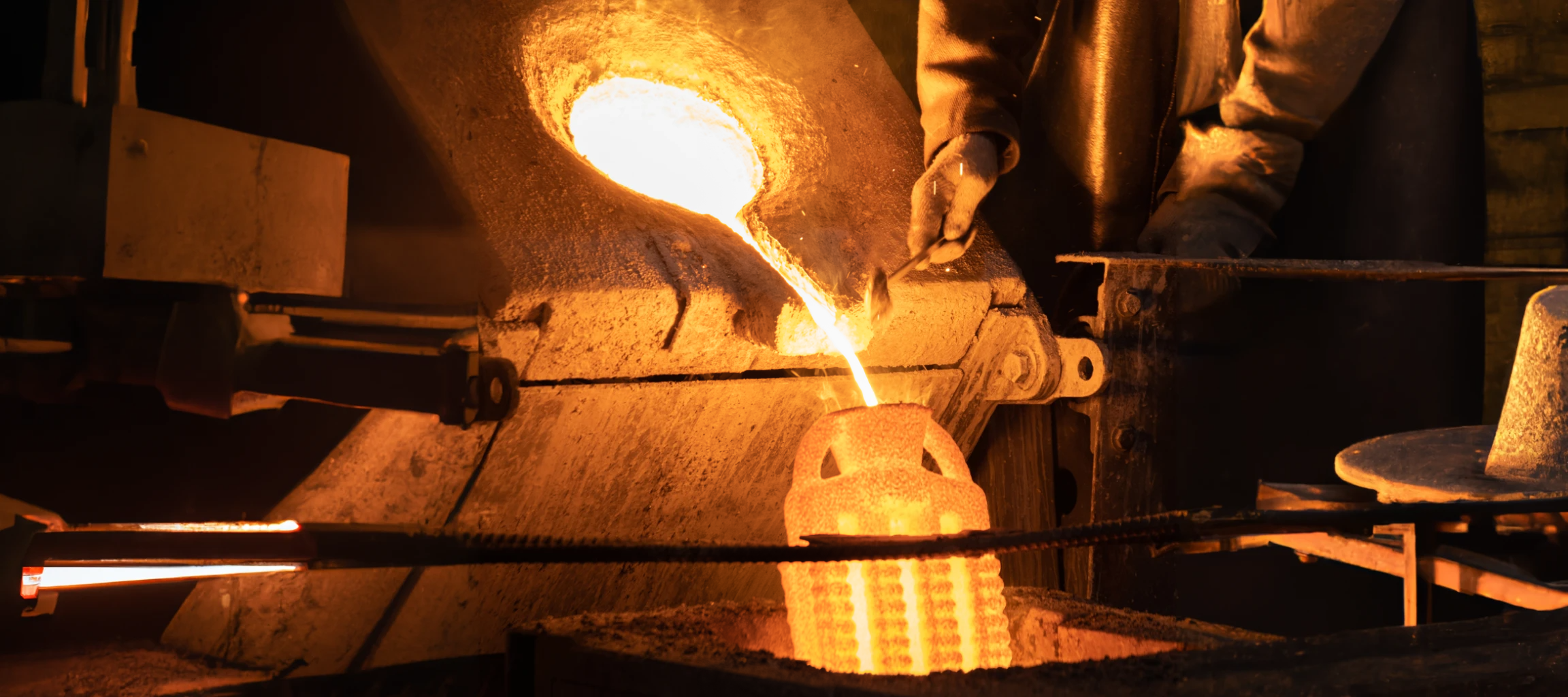
Feinguss
Präzisions- und Feinguss
Präzisions- und Feinguss werden eingesetzt, um Gussstücke mit höchster Maßgenauigkeit, komplexer Geometrie und bester Oberflächenqualität zu erhalten. Je nach Werkstoff, Gesamtstückzahl und Gestalt des Gussstückes wird das passende Gussverfahren nach wirtschaftlichen Aspekten ausgewählt.
Es können Gussstücke mit einer Masse von 0,001 kg bis zu mehreren Kilogramm hergestellt werden.
Einen großen Vorteil haben diese Verfahren darin, dass die fertig gegossenen Teile in der Regel einbaufertige Teile sind. Als Faustregel gilt, dass Präzisionsguss und Feinguss besonders wirtschaftlich sind, je komplizierter das Bauteil gestaltet ist oder je schwieriger und aufwendiger die Nachbearbeitung ist.
Verfügbare Werkstoffe
- Magnesiumlegierungen
- Aluminiumlegierungen
- Kupferlegierungen
- Eisenlegierungen
- Nickellegierungen
- Kobaltlegierungen
- weitere Werkstoffe auf Anfrage
Präzisions- und Feinguss
Präzisions- und Feinguss werden eingesetzt, um Gussstücke mit höchster Maßgenauigkeit, komplexer Geometrie und bester Oberflächenqualität zu erhalten. Je nach Werkstoff, Gesamtstückzahl und Gestalt des Gussstückes wird das passende Gussverfahren nach wirtschaftlichen Aspekten ausgewählt.
Es können Gussstücke mit einer Masse von 0,001 kg bis zu mehreren Kilogramm hergestellt werden.
Einen großen Vorteil haben diese Verfahren darin, dass die fertig gegossenen Teile in der Regel einbaufertige Teile sind. Als Faustregel gilt, dass Präzisionsguss und Feinguss besonders wirtschaftlich sind, je komplizierter das Bauteil gestaltet ist oder je schwieriger und aufwendiger die Nachbearbeitung ist.
Verfügbare Werkstoffe
- Magnesiumlegierungen
- Aluminiumlegierungen
- Kupferlegierungen
- Eisenlegierungen
- Nickellegierungen
- Kobaltlegierungen
- weitere Werkstoffe auf Anfrage
1. Modellherstellung
Flexible oder Feste Form
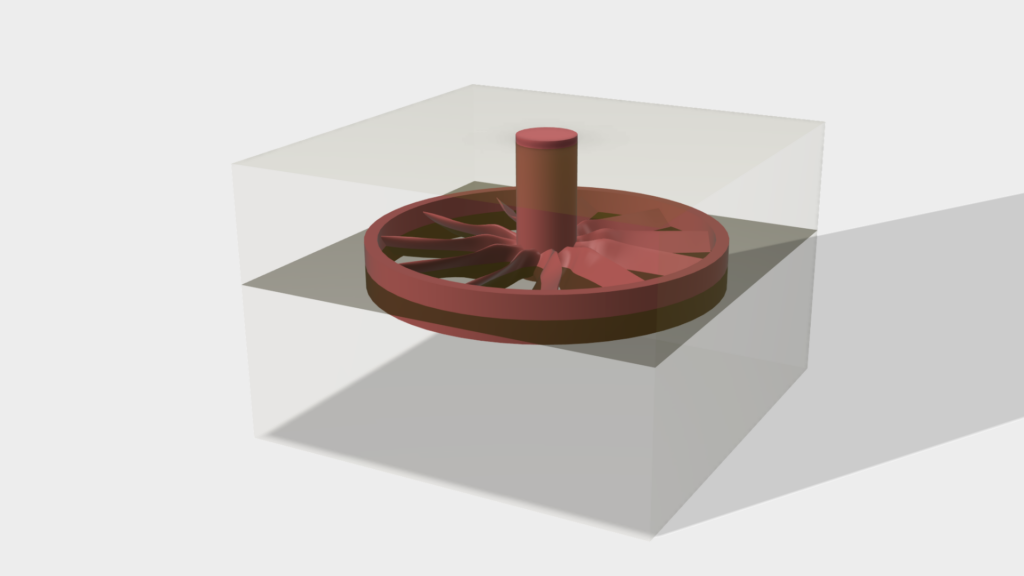
Rapid Prototyping
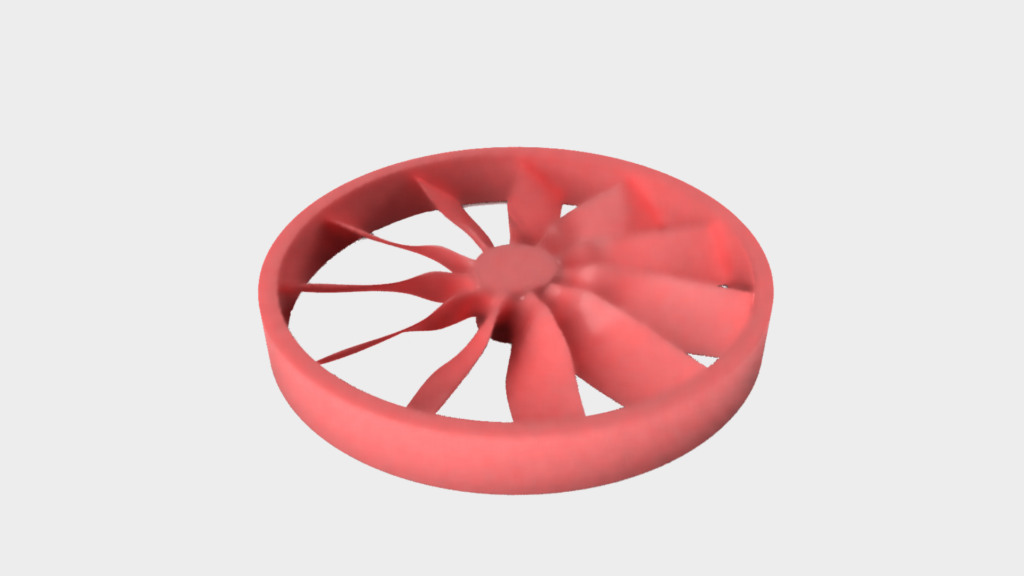
Zunächst wird eine mehrteilige Form hergestellt, aus der Wachsmodelle des zu fertigenden Bauteils gefertigt werden. Dazu wird die Form mit Wachs oder thermoplastischem Kunststoff ausgegossen und nach dem Erstarren kann das Modell aus der Form entfernt werden. Alternativ kann für Kleinserien auch die additive Fertigung eingesetzt werden.
2. Gusstraube aufbauen
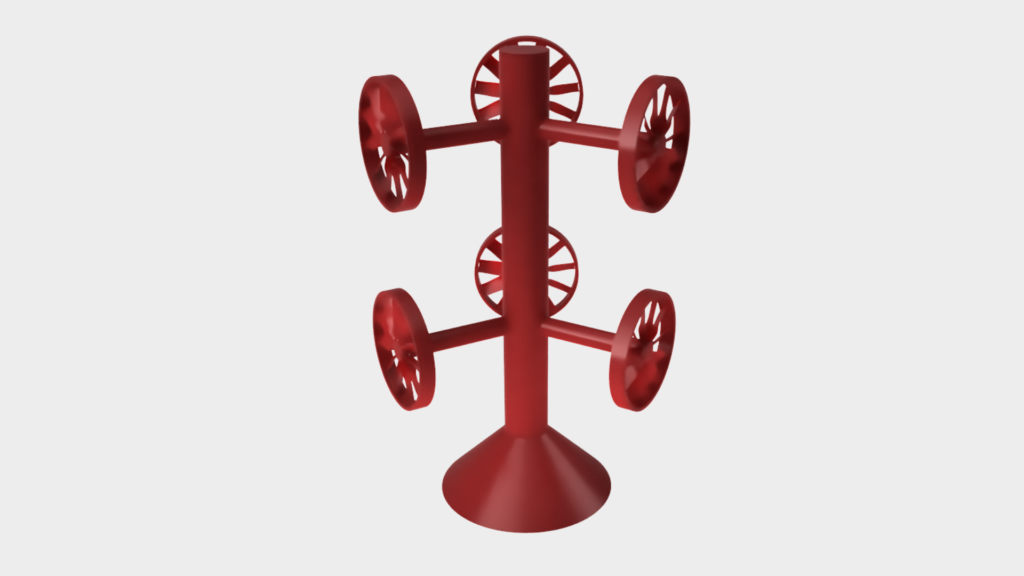
Die einzelnen Wachsmodelle werden anschließend zu einer Gusstraube montiert.
3. Gussform herstellen
Tauchen und Besanden
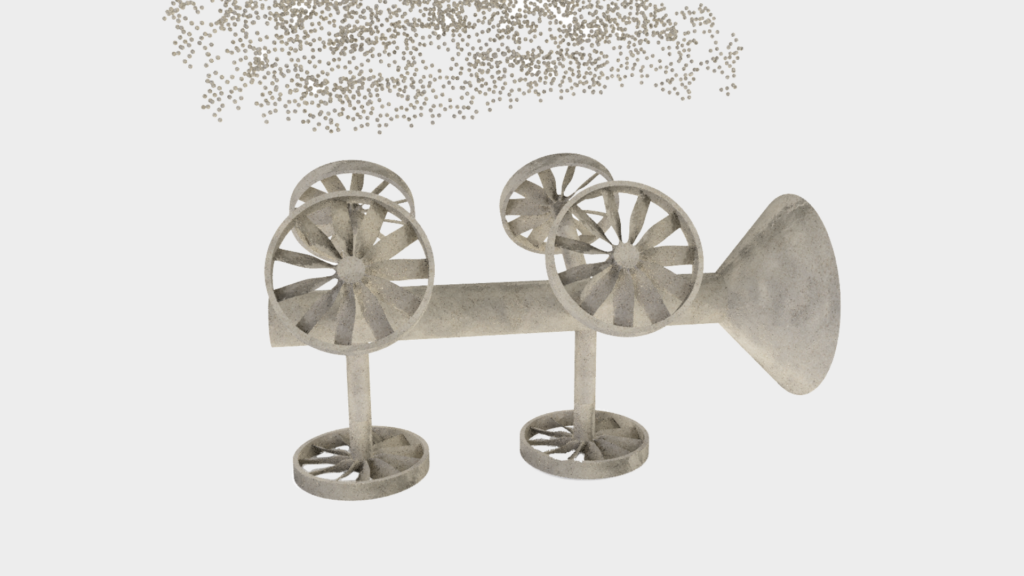
Die Gusstraube wird mehrmals in Schlicker getaucht und mit Formsand besandet. Dieser Prozess wird wiederholt, bis die gewünschte Maskenstärke erreicht ist.
Gipsform
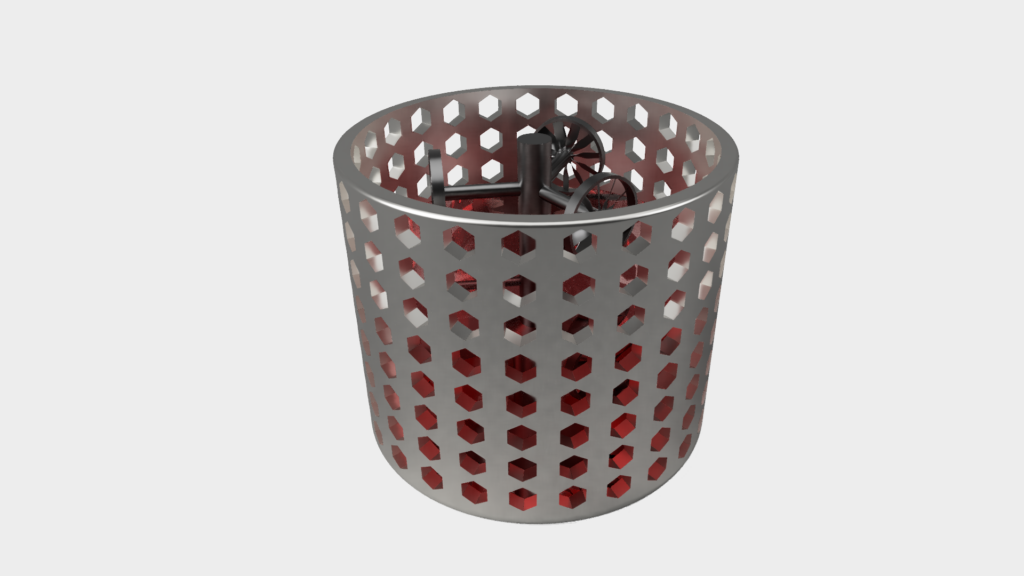
Die Gusstraube wird in eine Kuvette platziert und mit Formstoff ausgegossen.
4. Auswachsen und Brennen
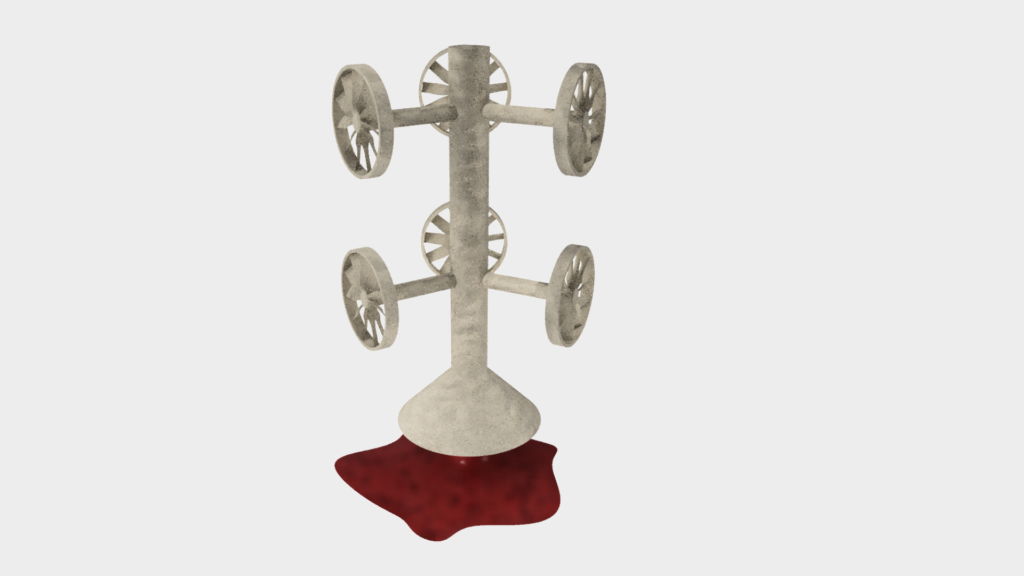
Als nächstes wird das Wachs oder der Kunststoff ausgeschmolzen und aufgefangen, um wiederverwendet zu werden. Zurück bleibt eine hohle Form.
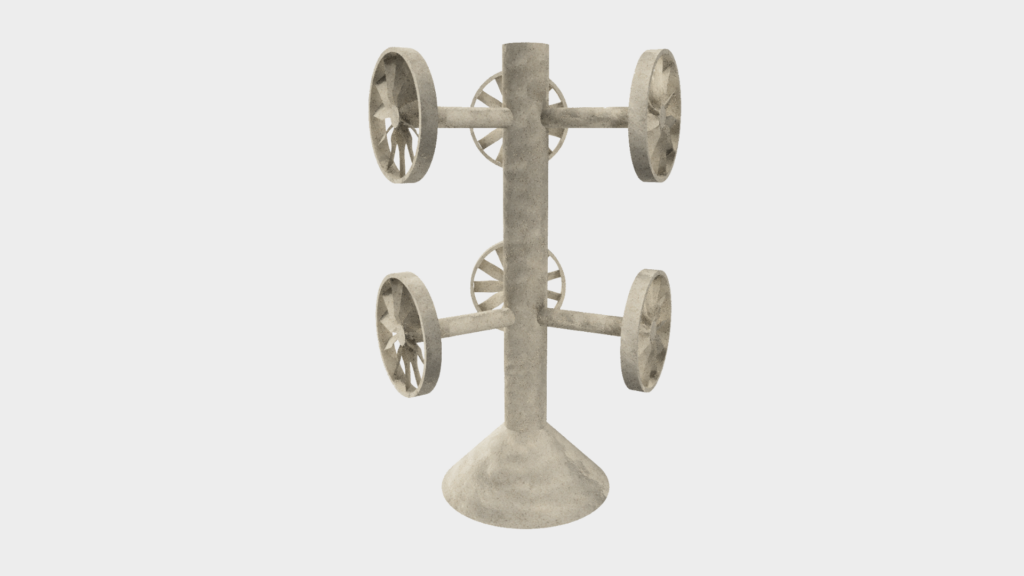
Die entstandene Form wird bei 800°C gebrannt, wodurch sie keramisch gebunden wird.
5. Gießen
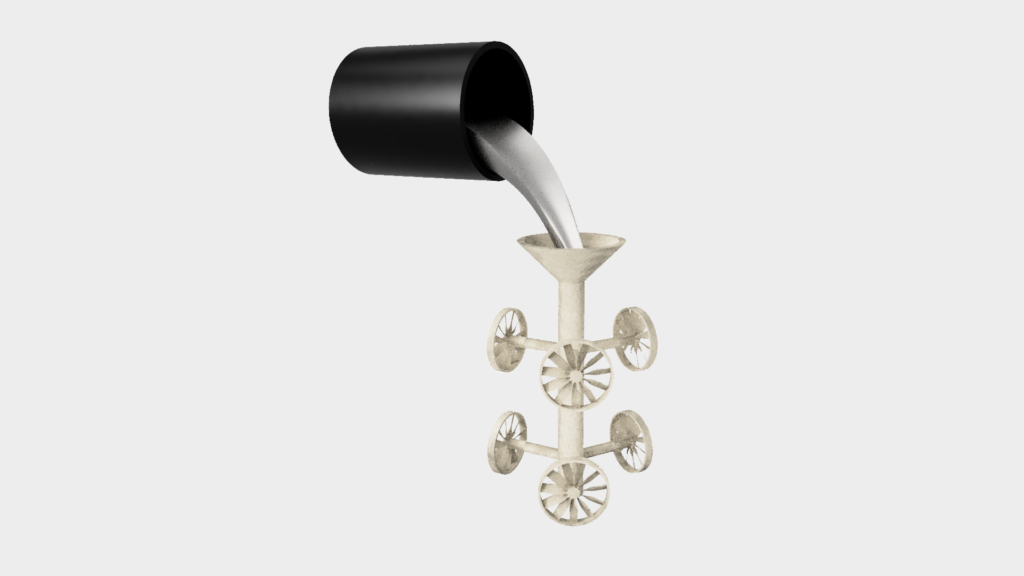
Anschließend wird die hohle Form mit geschmolzenem Metall ausgegossen, wodurch ein Bauteil mit den Maßen des ursprünglichen Modells entsteht.
6. Entformen
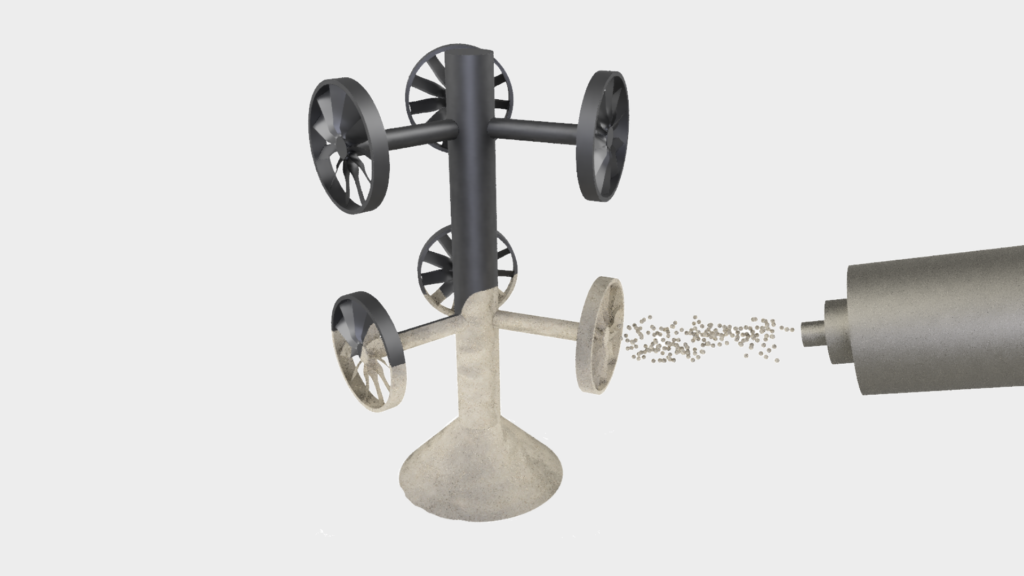
Das Bauteil wird nun entformt, wobei die Form zerstört wird. Anschließend werden die Bauteile durch mehrmaliges Sandstrahlen gereinigt, um alle Rückstände der Form zu beseitigen und nur das reine Bauteil zu hinterlassen.
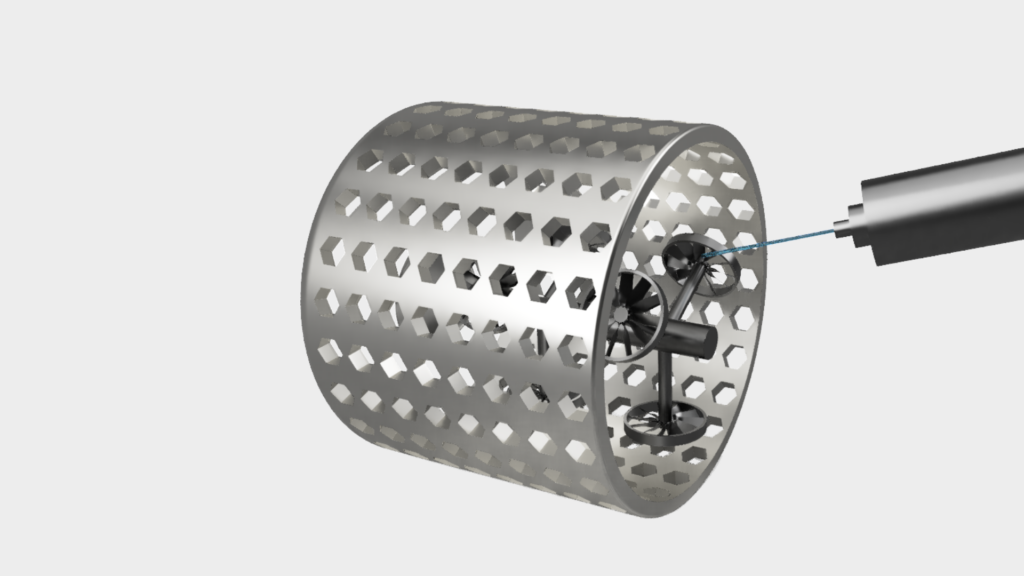
Das Bauteil wird nun mit Hilfe von Wasserstrahlen entformt.
7. Mechanisches Vorbearbeiten
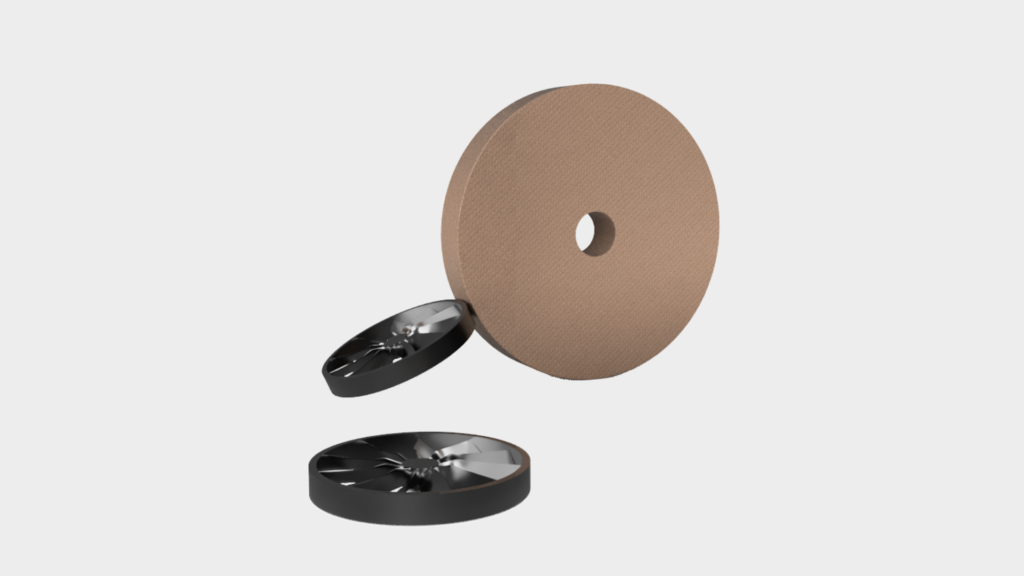
Zunächst werden die Bauteile an der ursprünglichen Verbindungsstelle abgesägt. Da die Oberfläche noch Angussreste aufweist, müssen diese durch passende Verfahren wie Schleifen oder Drehen entfernt werden.
8. Endbearbeitung
Je nach Kundenwunsch können nun weitere Bearbeitungsschritte durchgeführt werden. So können z.B. Bohrungen und Gewinde eingebracht, die Oberfläche verzinkt oder auch eine Wärmebehandlung durchgeführt werden. In diesem Schritt werden die speziellen Kundenwünsche und -anforderungen umgesetzt.
Bohren, Fräsen, Drehen
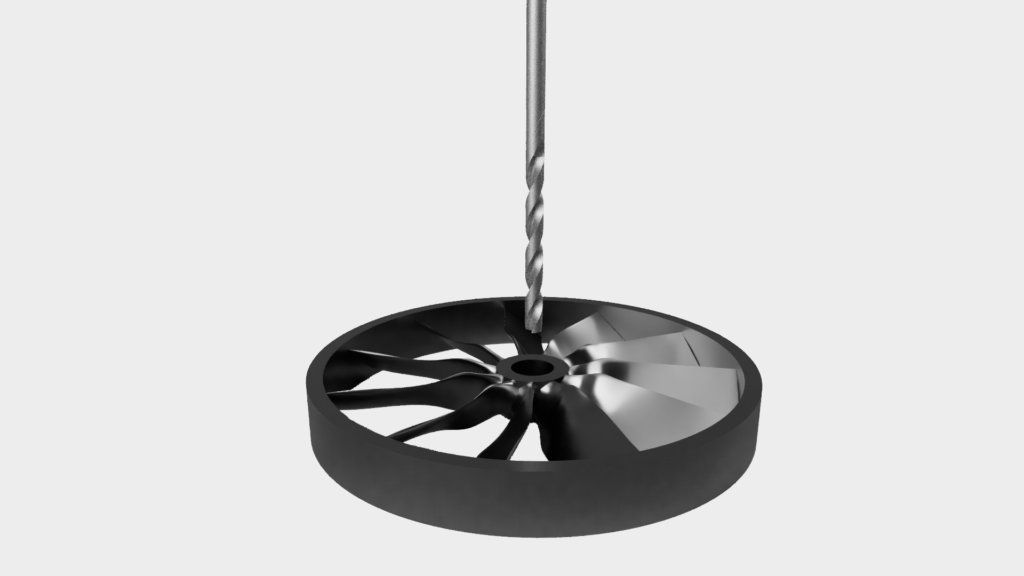
Oberflächenveredelung
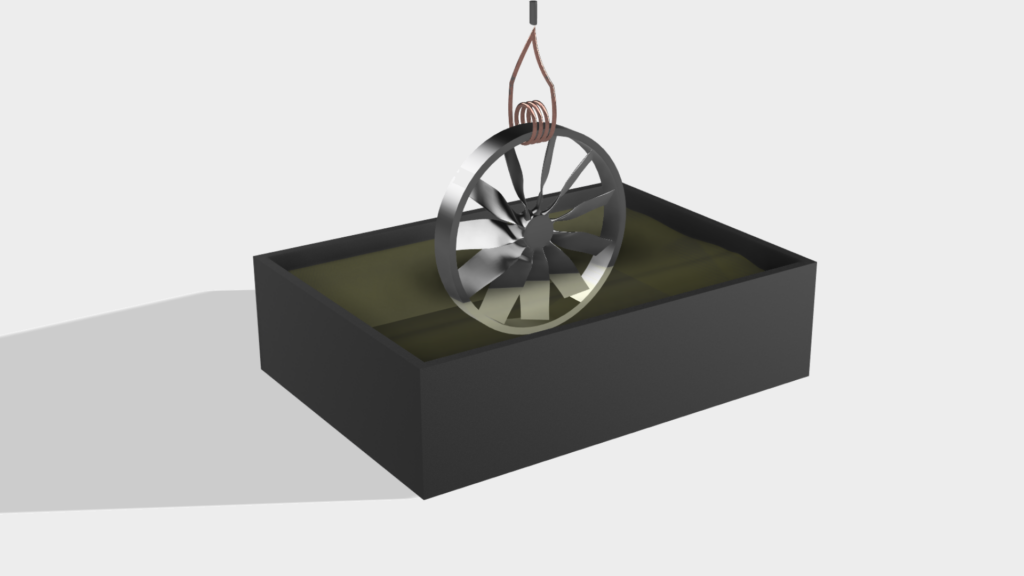
Wärmebehandlung
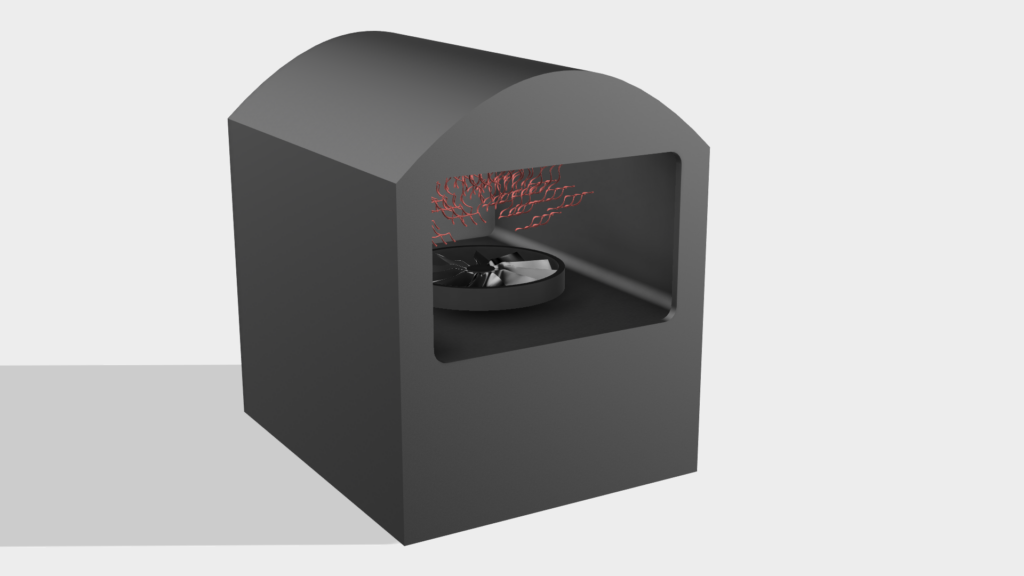
9. Qualitätskontrolle
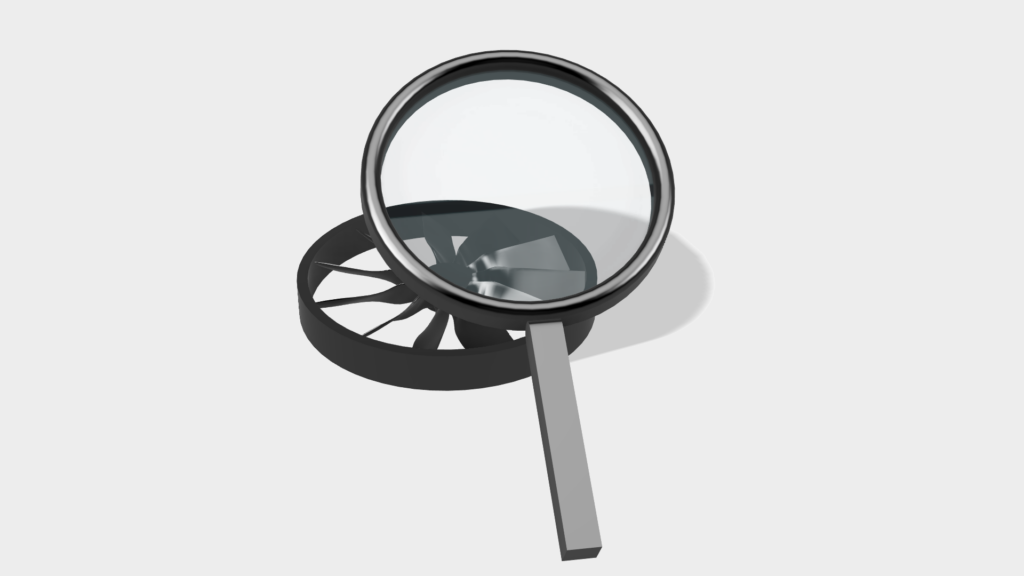
Im letzten Schritt wird das Bauteil noch einer Qualitätskontrolle unterzogen. Dabei wird es gewissenhaft auf Beschädigungen oder Mängel geprüft, sodass alle Bauteile unseren hohen Qualitätsanforderungen entsprechen. Mit diesem Schritt ist der gesamte Prozess abgeschlossen und das Bauteil ist fertig für den Einsatz.
1. Modellherstellung
Flexible oder Feste Form
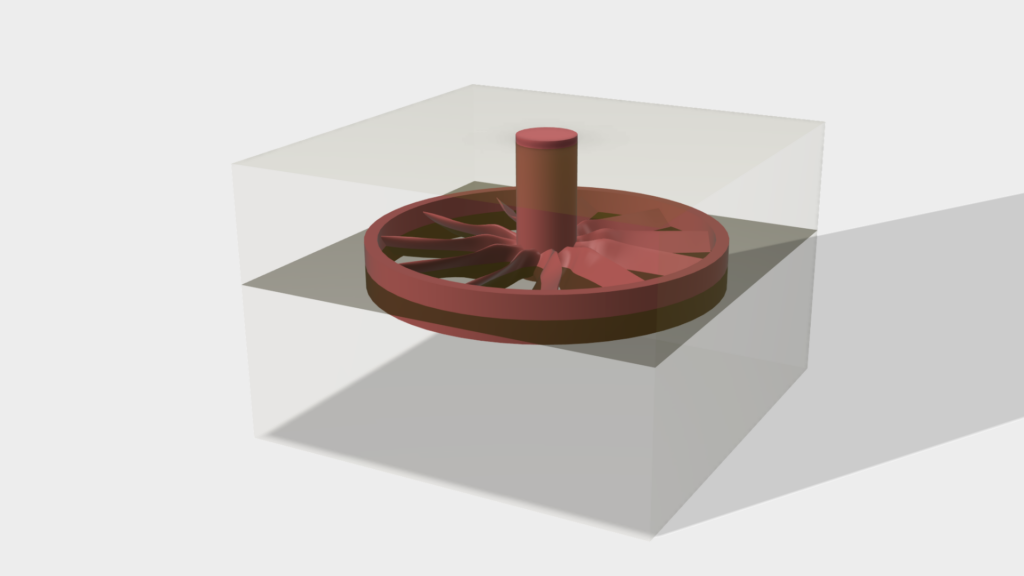
Rapid Prototyping
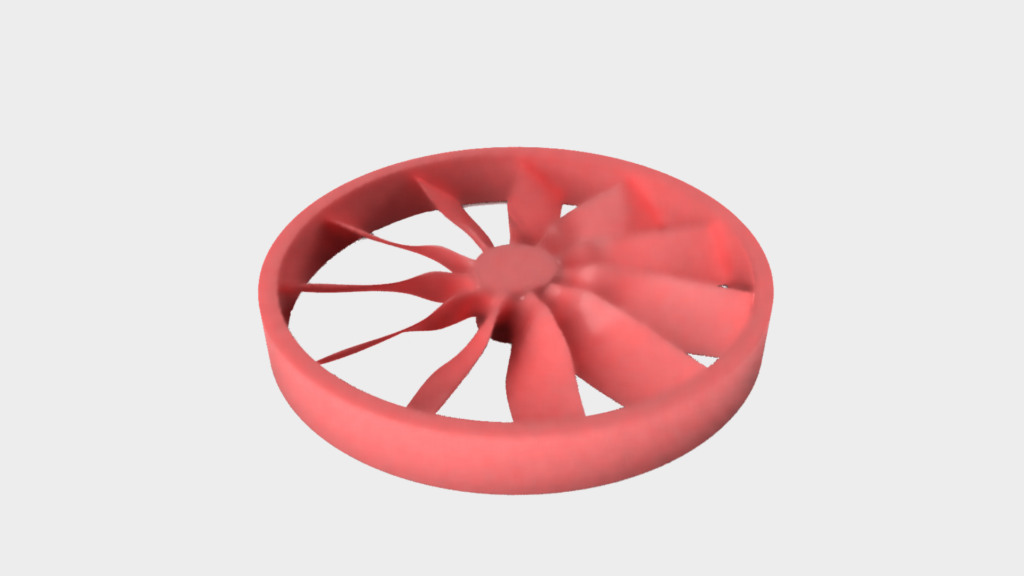
Zunächst wird eine mehrteilige Form hergestellt, aus der Wachsmodelle des zu fertigenden Bauteils gefertigt werden. Dazu wird die Form mit Wachs oder thermoplastischem Kunststoff ausgegossen und nach dem Erstarren kann das Modell aus der Form entfernt werden. Alternativ kann für Kleinserien auch die additive Fertigung eingesetzt werden.
2. Gusstraube aufbauen
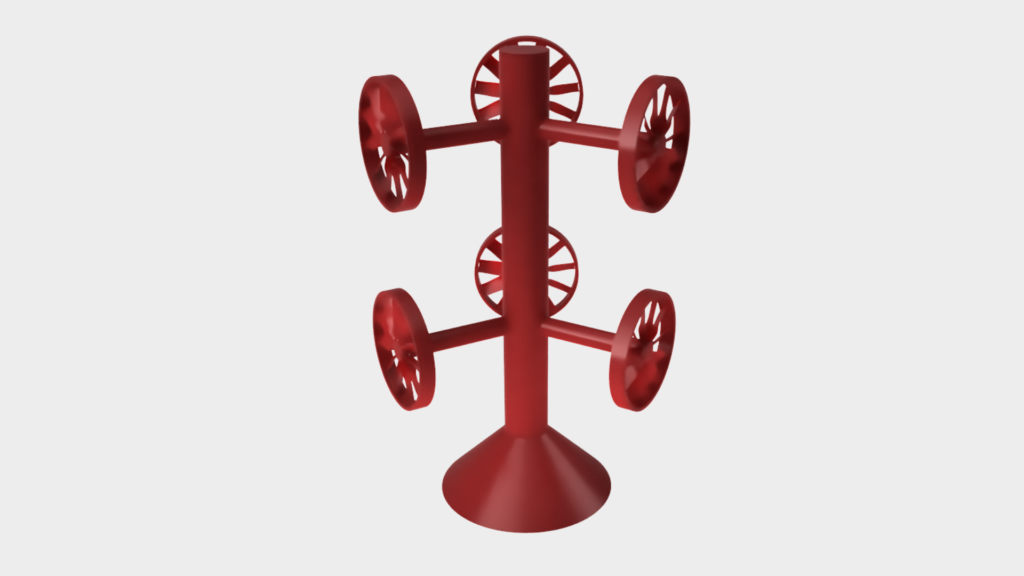
Die einzelnen Wachsmodelle werden anschließend zu einer Gusstraube montiert.
3. Gussform herstellen
Tauchen und Besanden
Die Gusstraube wird mehrmals in Schlicker getaucht und mit Formsand besandet. Dieser Prozess wird wiederholt, bis die gewünschte Maskenstärke erreicht ist.
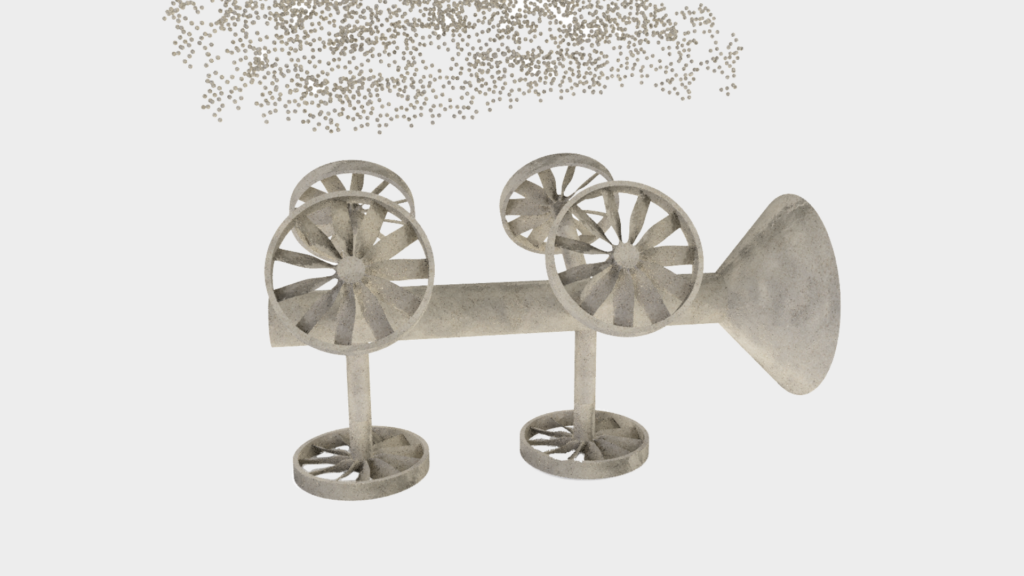
Gipsform
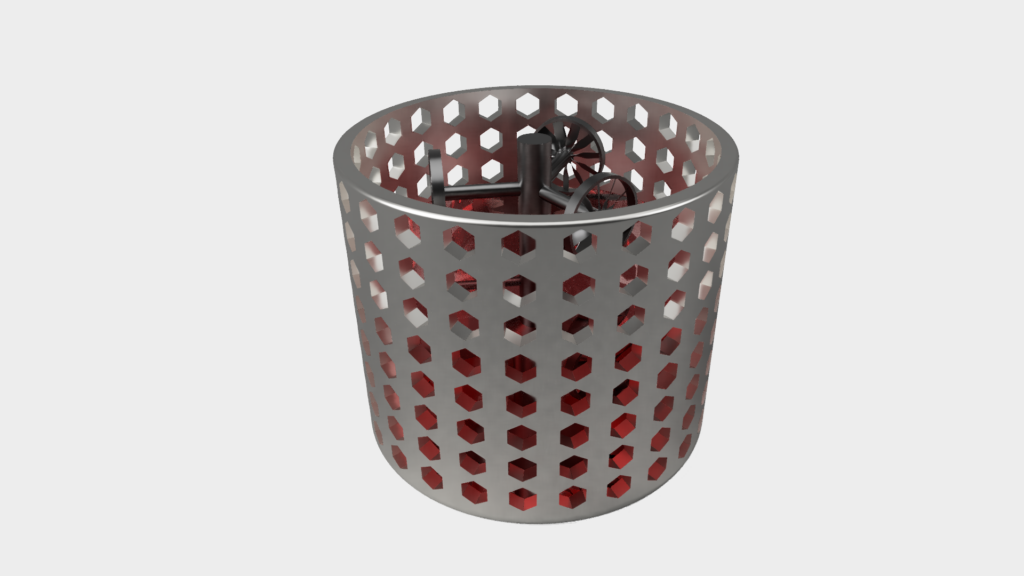
Die Gusstraube wird in eine Kuvette platziert und mit Formstoff ausgegossen.
4. Auswachsen und Brennen
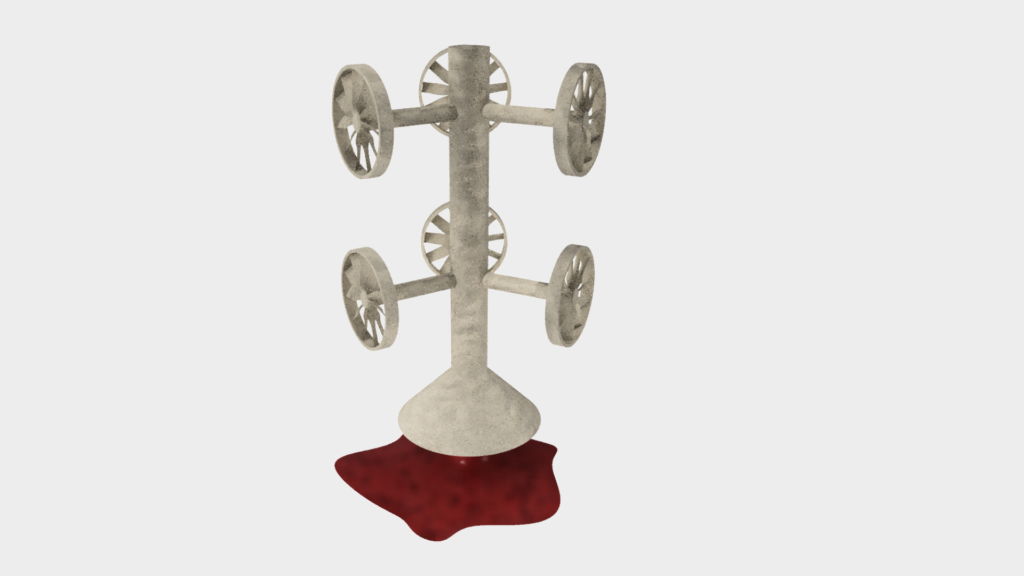
Als nächstes wird das Wachs oder der Kunststoff ausgeschmolzen und aufgefangen, um wiederverwendet zu werden. Zurück bleibt eine hohle Form.
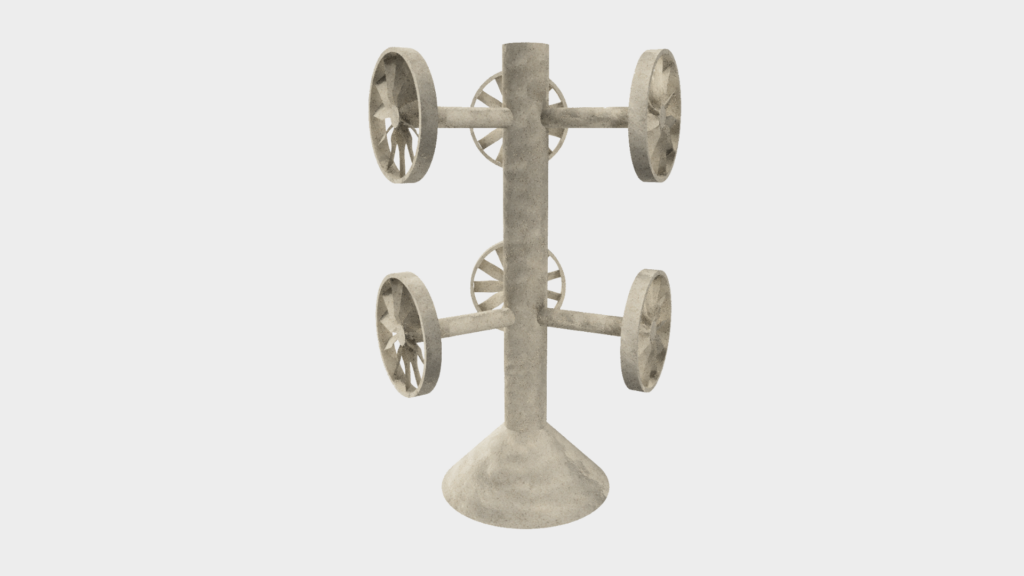
Die entstandene Form wird bei 800°C gebrannt, wodurch sie keramisch gebunden wird.
5. Gießen
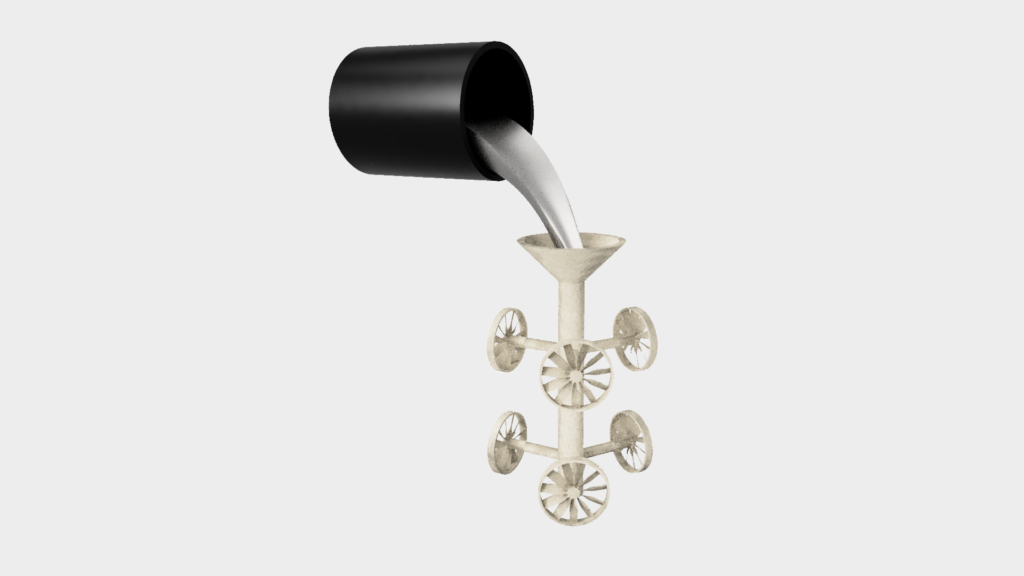
Anschließend wird die hohle Form mit geschmolzenem Metall ausgegossen, wodurch ein Bauteil mit den Maßen des ursprünglichen Modells entsteht.
6. Entformen
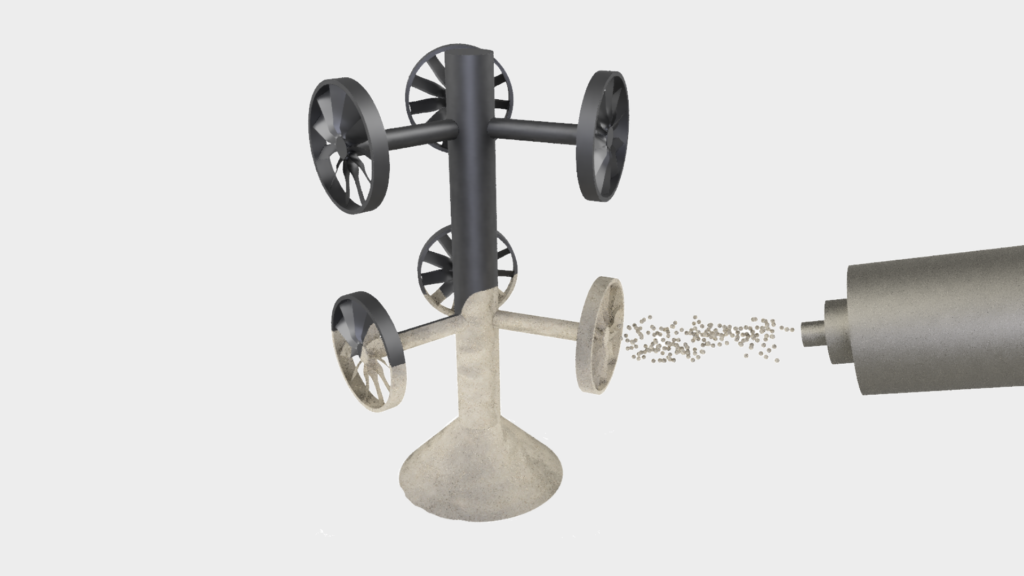
Das Bauteil wird nun entformt, wobei die Form zerstört wird. Anschließend werden die Bauteile durch mehrmaliges Sandstrahlen gereinigt, um alle Rückstände der Form zu beseitigen und nur das reine Bauteil zu hinterlassen.
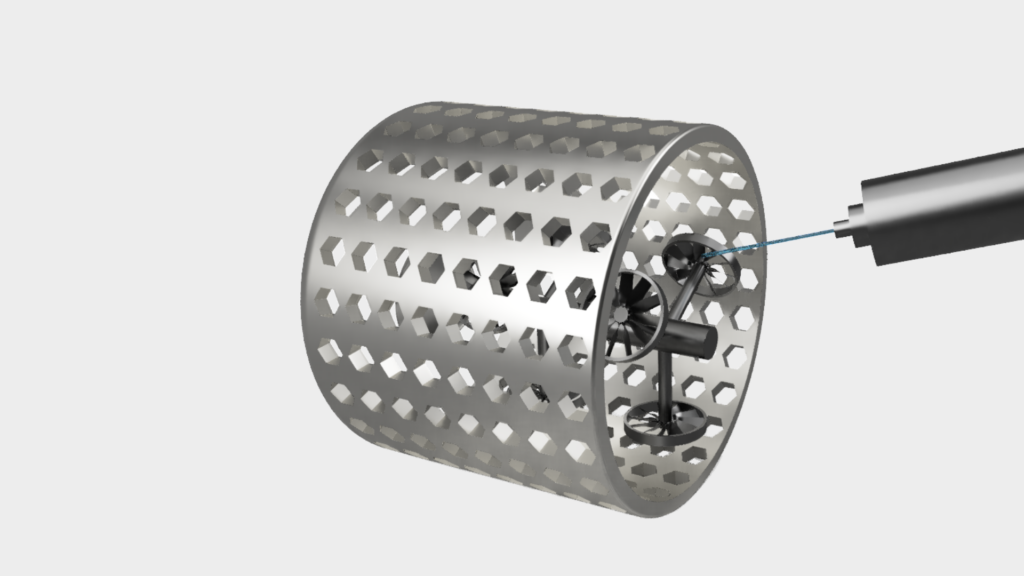
Das Bauteil wird nun mit Hilfe von Wasserstrahlen entformt.
7. Mechanisches Vorbearbeiten
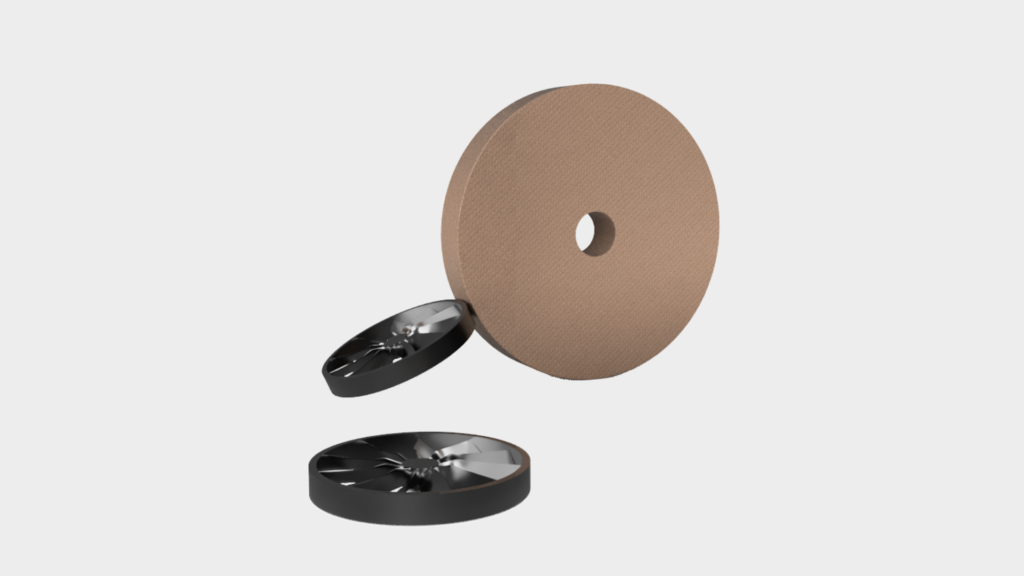
Zunächst werden die Bauteile an der ursprünglichen Verbindungsstelle abgesägt. Da die Oberfläche noch Angussreste aufweist, müssen diese durch passende Verfahren wie Schleifen oder Drehen entfernt werden.
8. Endbearbeitung
Je nach Kundenwunsch können nun weitere Bearbeitungsschritte durchgeführt werden. So können z.B. Bohrungen und Gewinde eingebracht, die Oberfläche verzinkt oder auch eine Wärmebehandlung durchgeführt werden. In diesem Schritt werden die speziellen Kundenwünsche und -anforderungen umgesetzt.
Bohren, Fräsen, Drehen
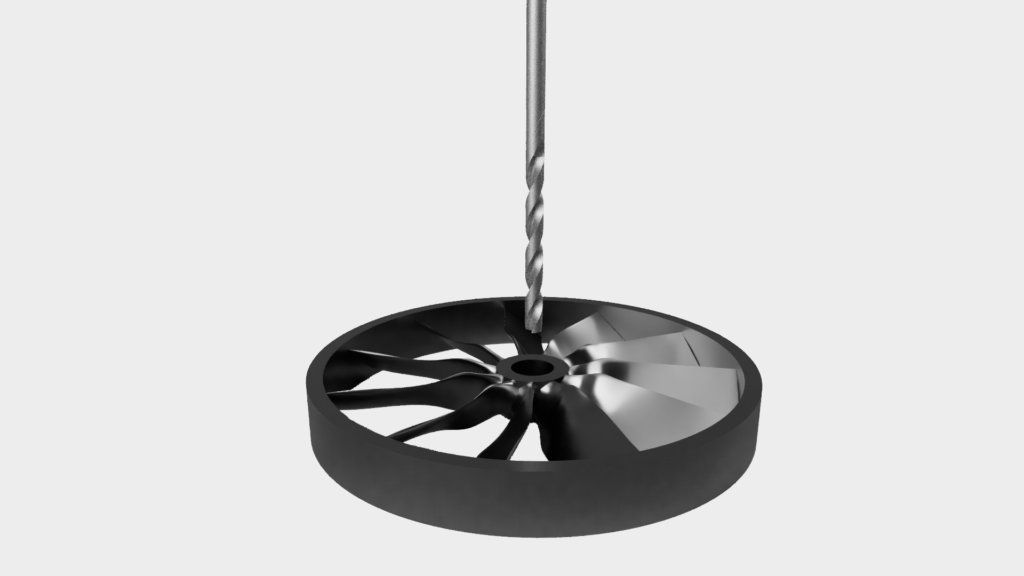
Oberflächenveredelung
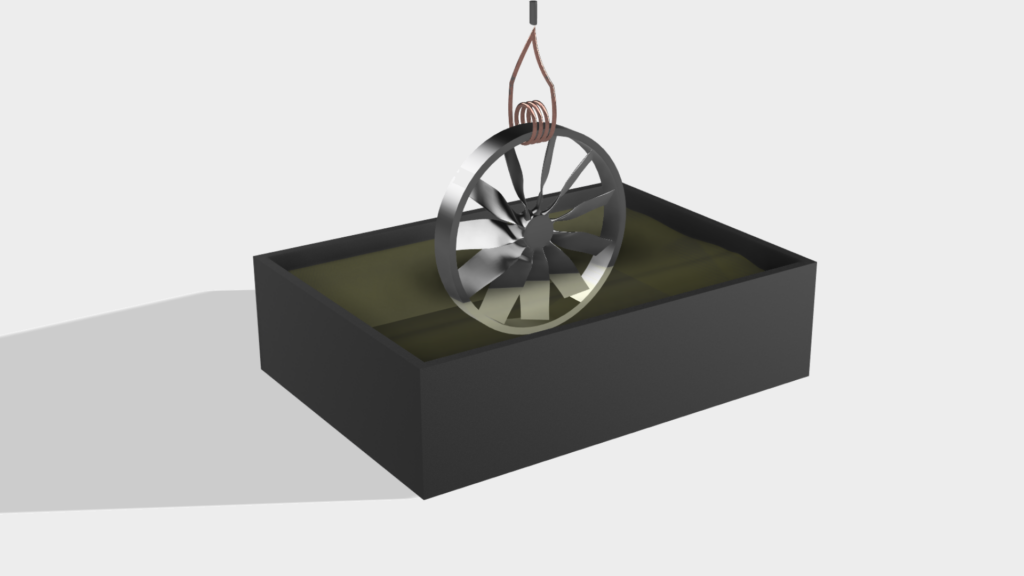
Wärmebehandlung
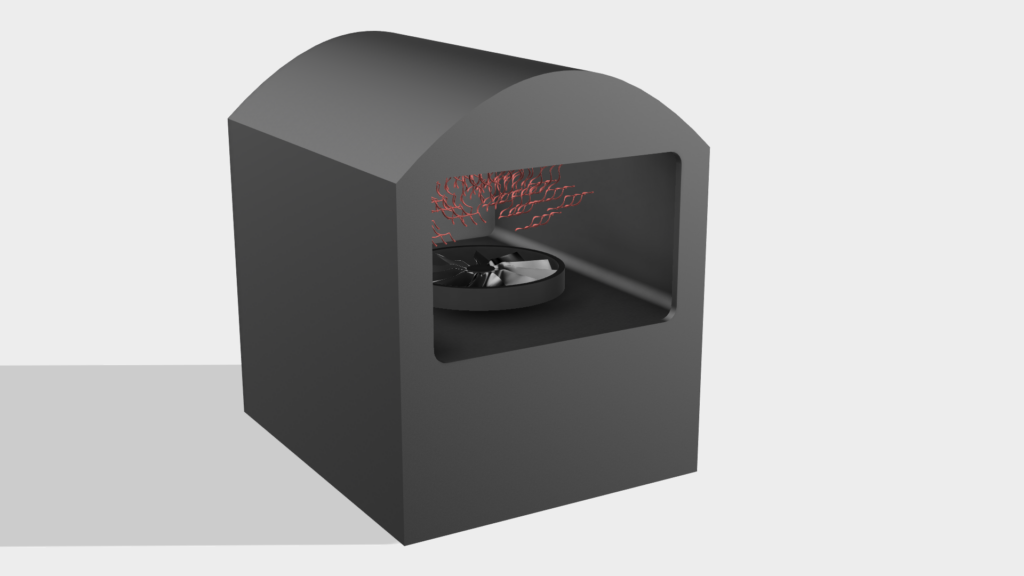
9. Qualitätskontrolle
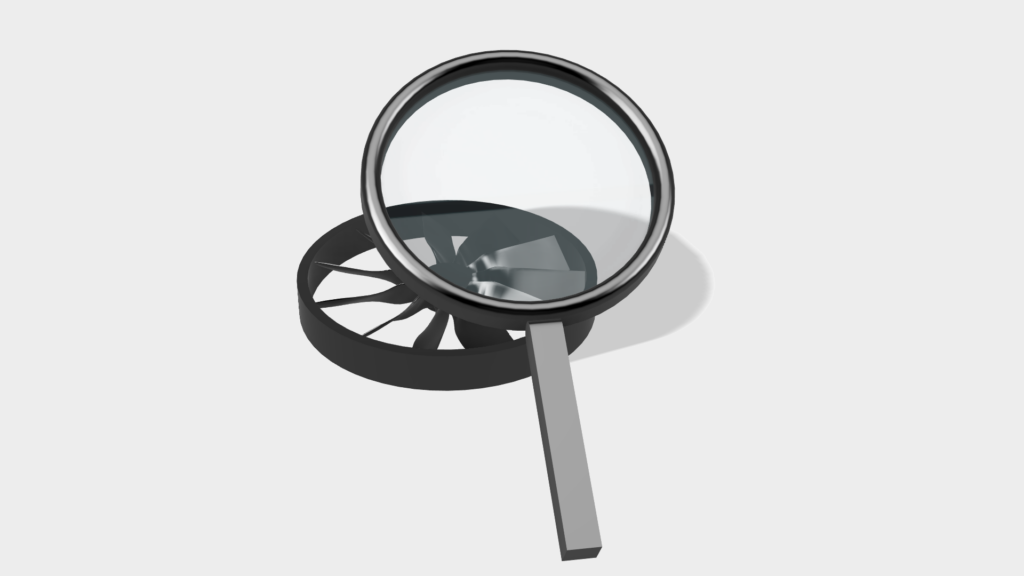
Im letzten Schritt wird das Bauteil noch einer Qualitätskontrolle unterzogen. Dabei wird es gewissenhaft auf Beschädigungen oder Mängel geprüft, sodass alle Bauteile unseren hohen Qualitätsanforderungen entsprechen. Mit diesem Schritt ist der gesamte Prozess abgeschlossen und das Bauteil ist fertig für den Einsatz.