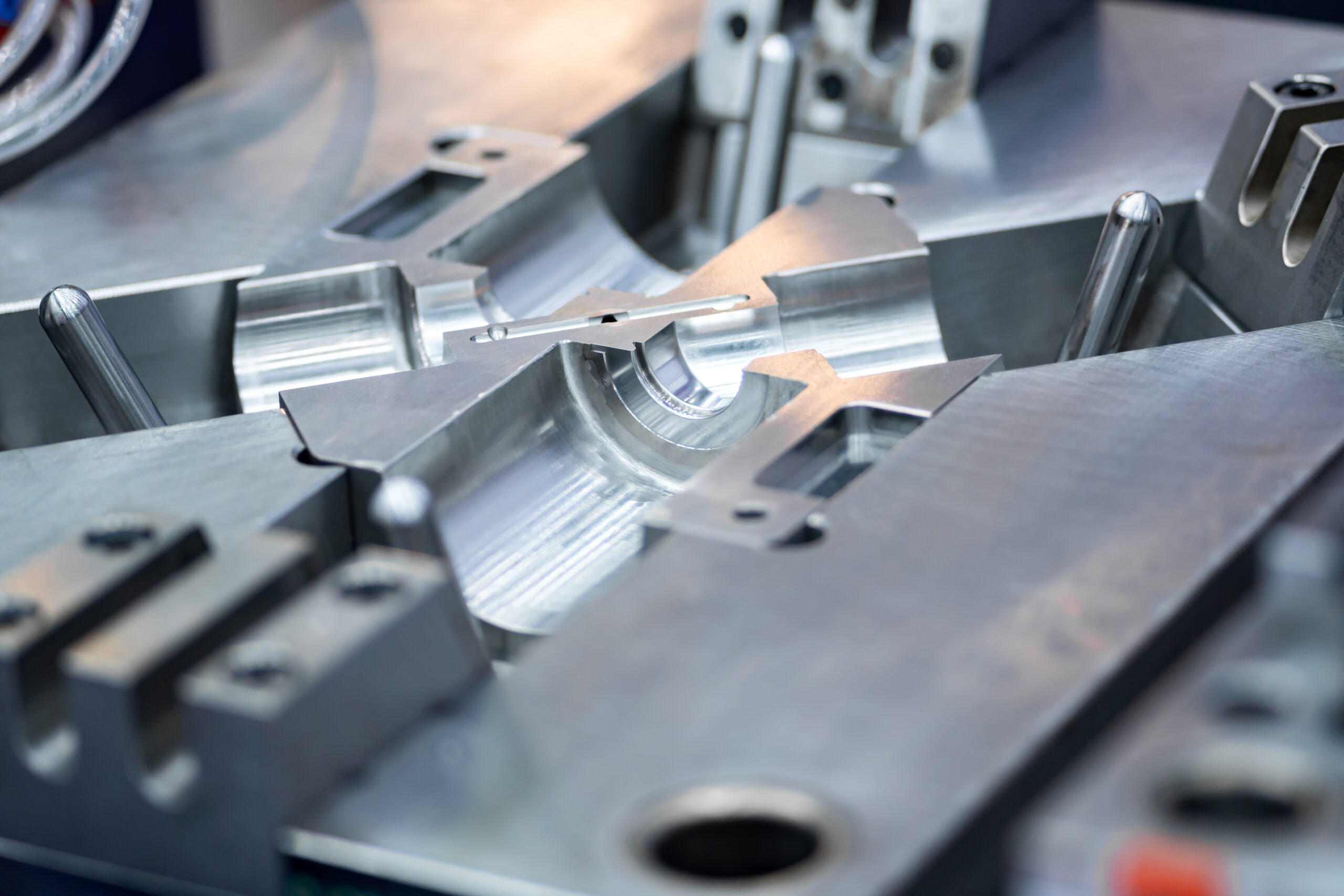
Die Casting
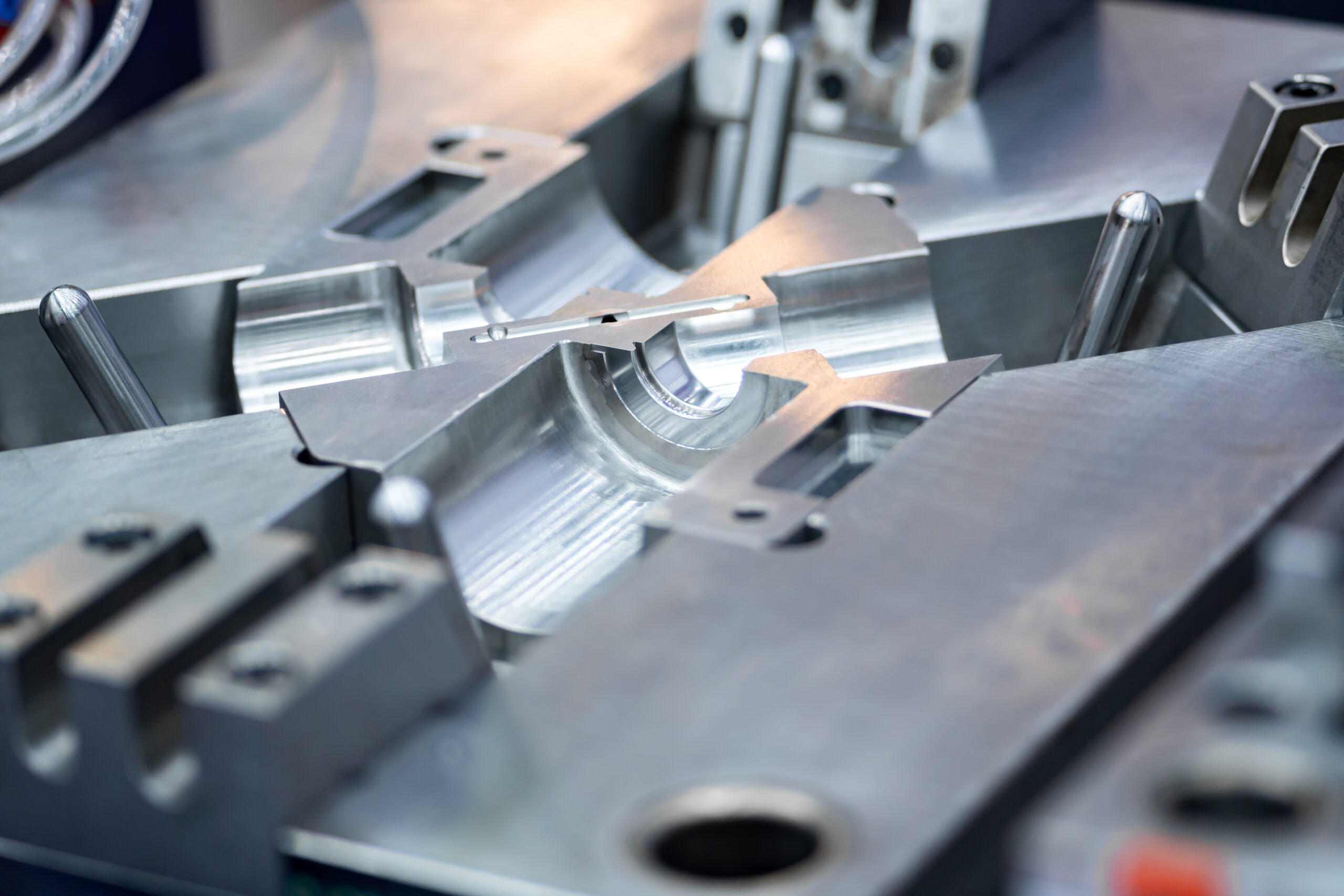
Die Casting
Die Casting
Die casting is a process used to manufacture parts from aluminum, zinc and magnesium alloys. It offers many advantages that make it a popular choice in various industries.
The benefits of die casting include high strength, durability, corrosion resistance and excellent surface quality. Die casting is very efficient and makes it possible to produce complex parts in large quantities.
Aluminum is a widely used material. It is easily recyclable and environmentally friendly. Aluminum die casting is therefore an ideal choice for applications where weight reduction and sustainability play a role.
Overall, aluminum die casting offers many advantages and is an economical solution for the production of parts in many industries. If you would like to learn more about aluminum die casting or have any questions, please do not hesitate to contact us. We are at your disposal.
Available materials
- Aluminum alloys
- Zinc alloys
- Magnesium alloys
Die Casting
Die casting is a process used to manufacture parts from aluminum, zinc and magnesium alloys. It offers many advantages that make it a popular choice in various industries.
The benefits of die casting include high strength, durability, corrosion resistance and excellent surface quality. Die casting is very efficient and makes it possible to produce complex parts in large quantities.
Aluminum is a widely used material. It is easily recyclable and environmentally friendly. Aluminum die casting is therefore an ideal choice for applications where weight reduction and sustainability play a role.
Overall, aluminum die casting offers many advantages and is an economical solution for the production of parts in many industries. If you would like to learn more about aluminum die casting or have any questions, please do not hesitate to contact us. We are at your disposal.
Available materials
- Aluminum alloys
- Zinc alloys
- Magnesium alloys
1. Empty mold
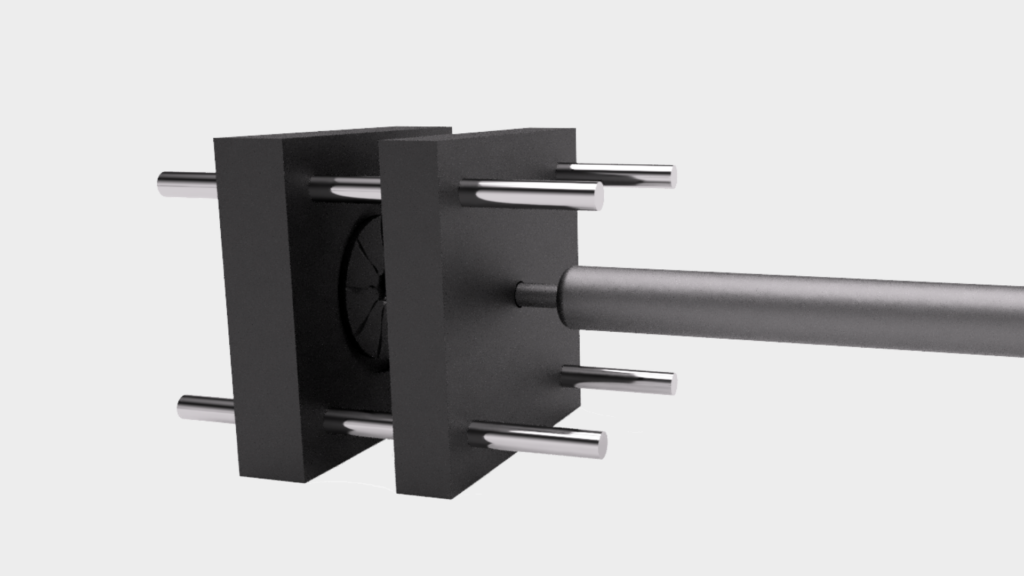
First, an empty mold is inserted into the die casting machine. This is the mold into which the liquid metal is later injected.
2. Injection process
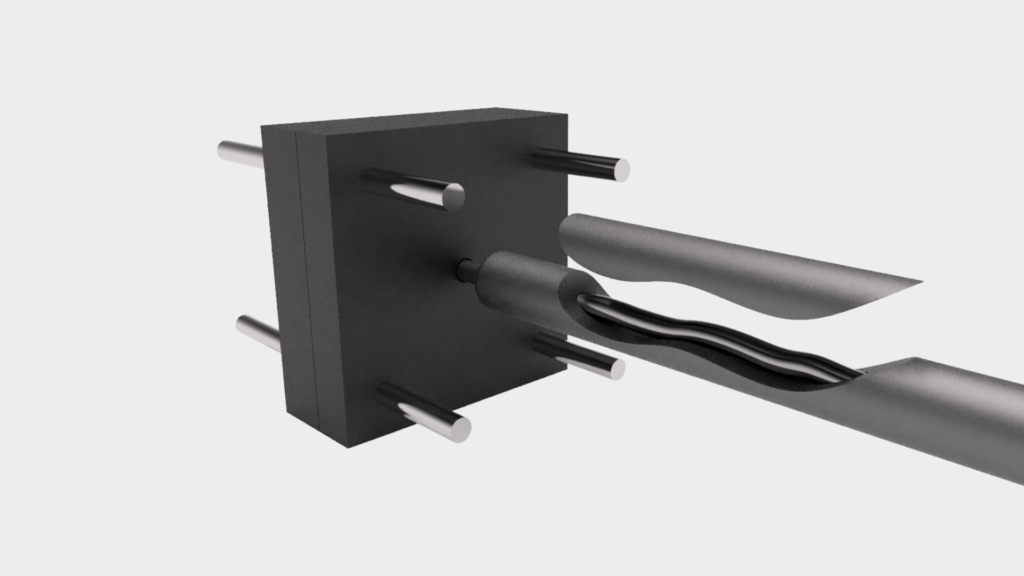
The mold is now closed. The liquid metal is then injected into the cavity under pressure.
3. Demolding
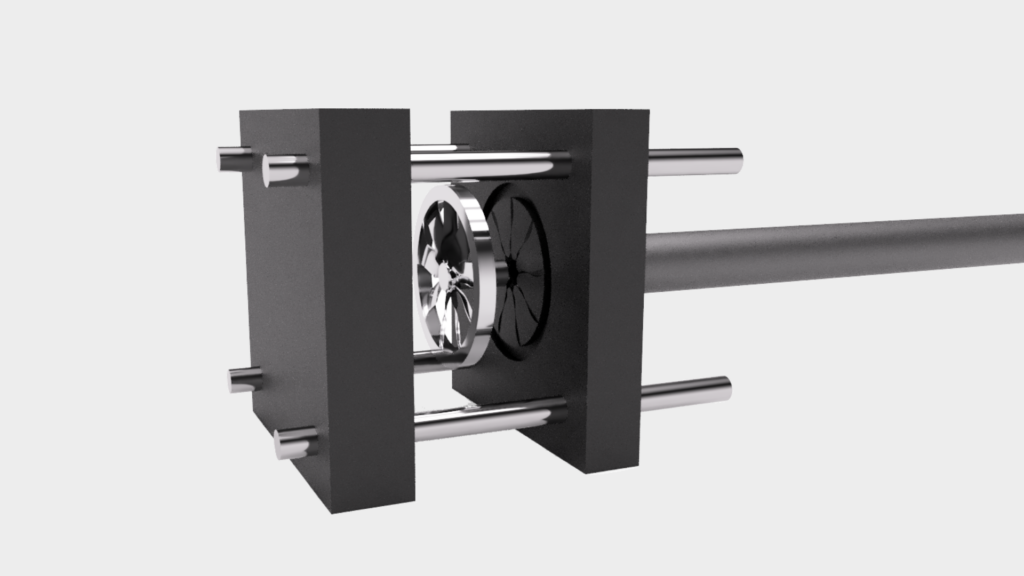
After cooling, the component is demolded. To do this, the mold is opened and the component is pressed out.
4. Mechanical pre-machining
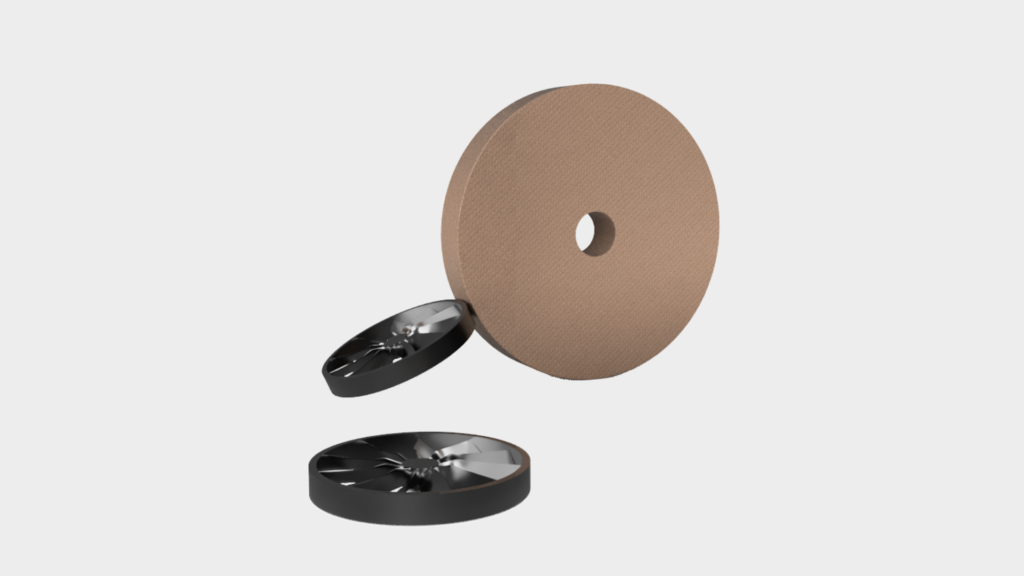
First, the components are sawn off at the original connection point. As the surface still has sprue residues, these must be removed using suitable methods such as grinding or turning.
5. Finishing
Depending on customer requirements, further processing steps can now be carried out. For example, holes and threads can be drilled, the surface galvanized or heat treated. In this step, the customer’s specific wishes and requirements are implemented.
Drilling, milling, lathing
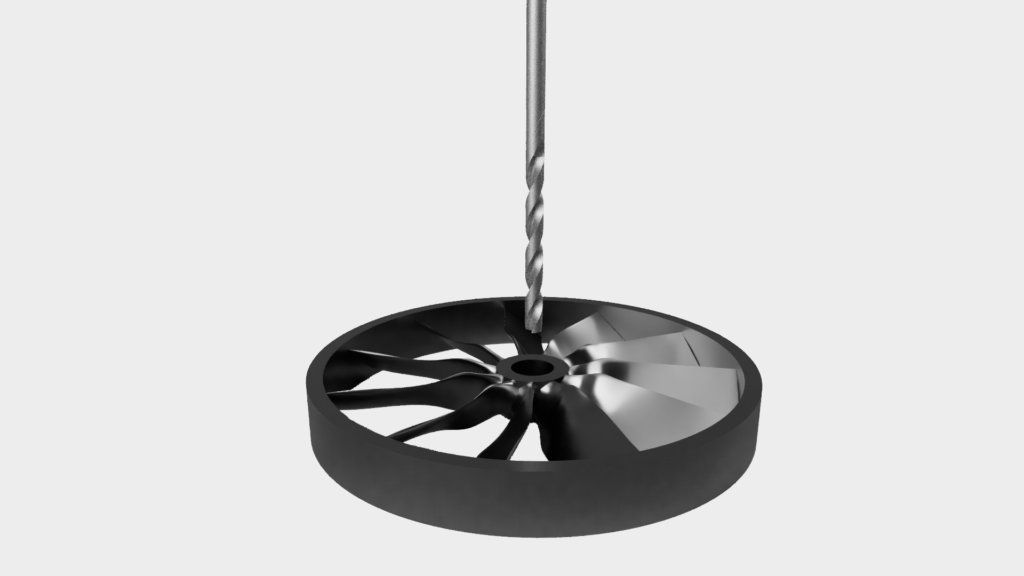
Surface refinement
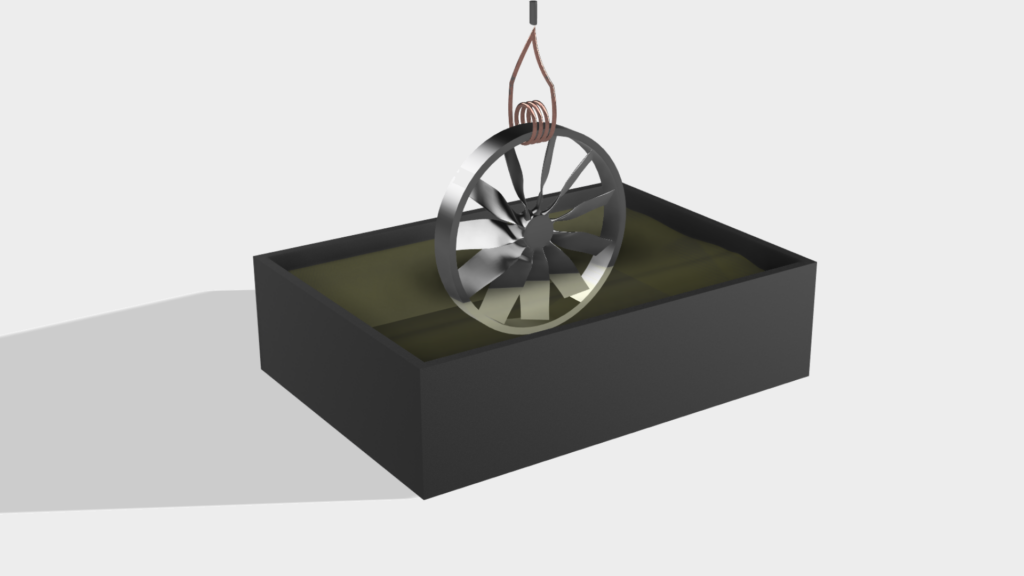
Heat treatment
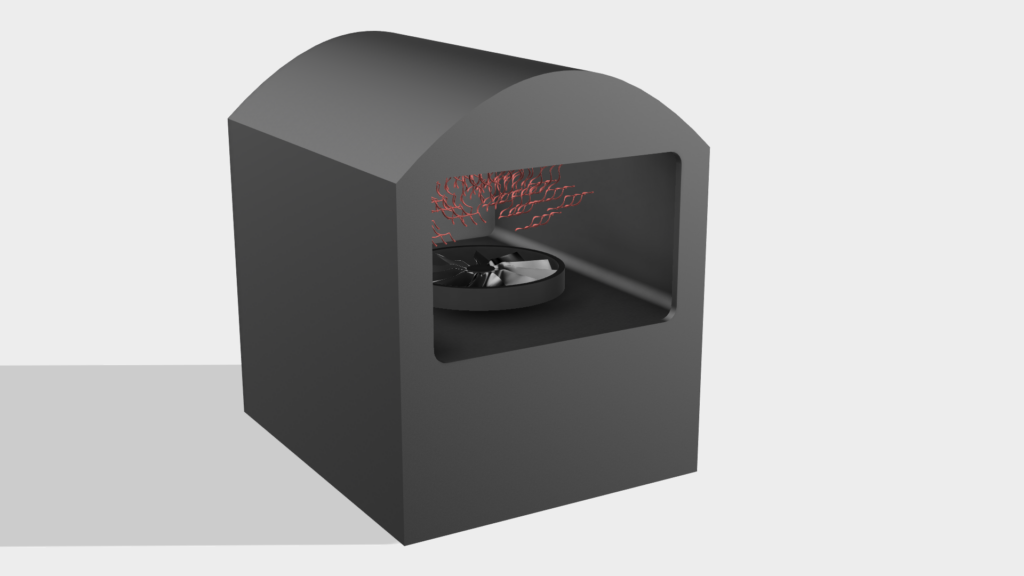
6. Quality control
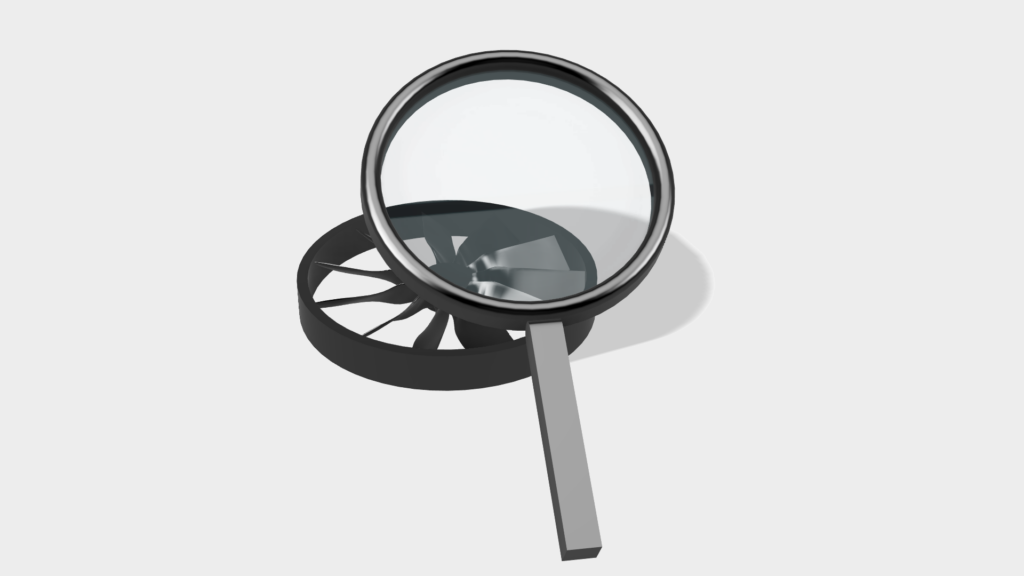
In the final step, the component is subjected to a quality check. It is carefully checked for damage or defects so that all components meet our high quality requirements. This step completes the entire process and the component is ready for use.
1. Empty mold
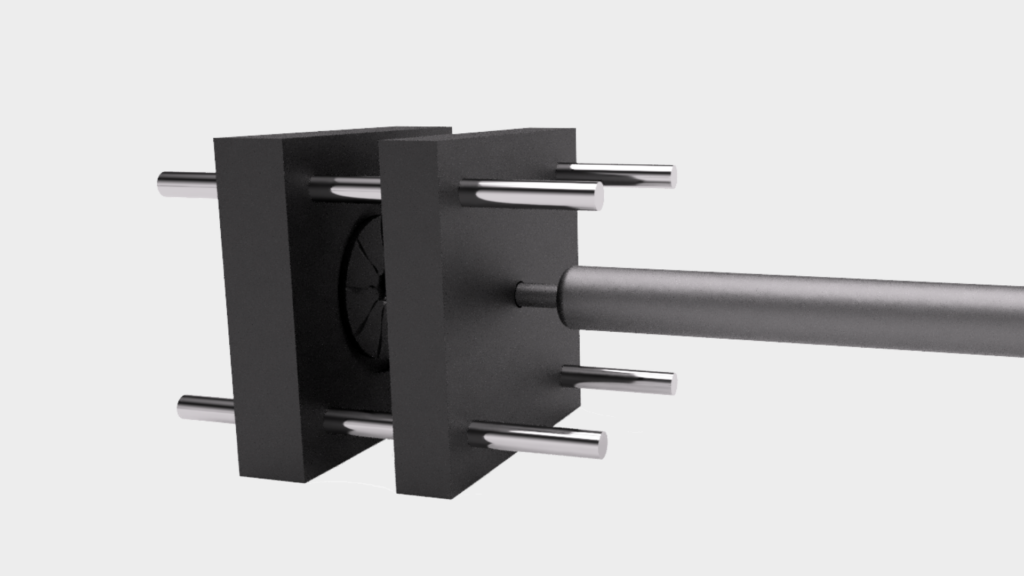
First, an empty mold is inserted into the die casting machine. This is the mold into which the liquid metal is later injected.
2. Injection process
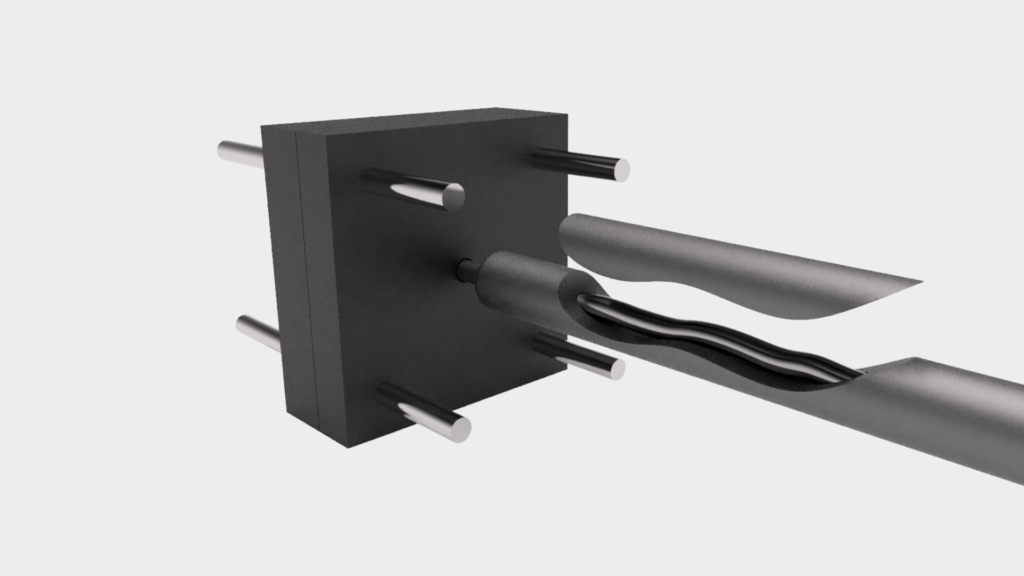
The mold is now closed. The liquid metal is then injected into the cavity under pressure.
3. Demolding
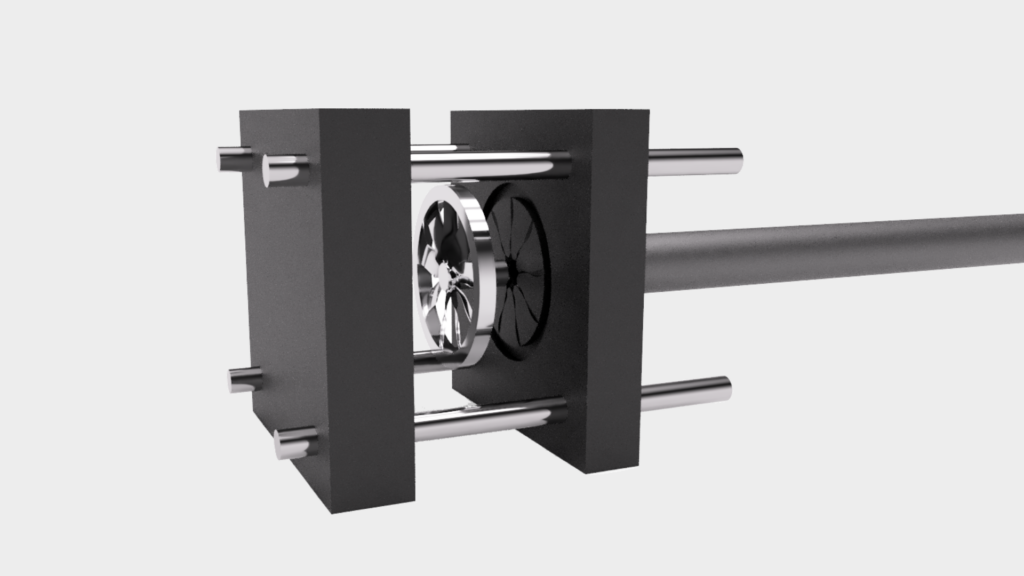
After cooling, the component is demolded. To do this, the mold is opened and the component is pressed out.
4. Mechanical pre-machining
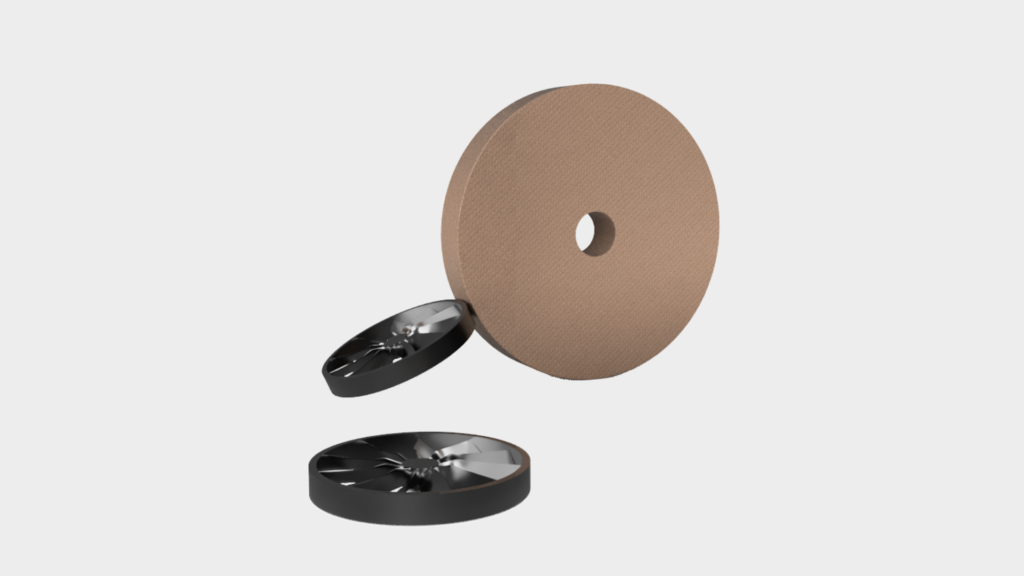
First, the components are sawn off at the original connection point. As the surface still has sprue residues, these must be removed using suitable methods such as grinding or turning.
5. Finishing
Depending on customer requirements, further processing steps can now be carried out. For example, holes and threads can be drilled, the surface galvanized or heat treated. In this step, the customer’s specific wishes and requirements are implemented.
Drilling, milling, lathing
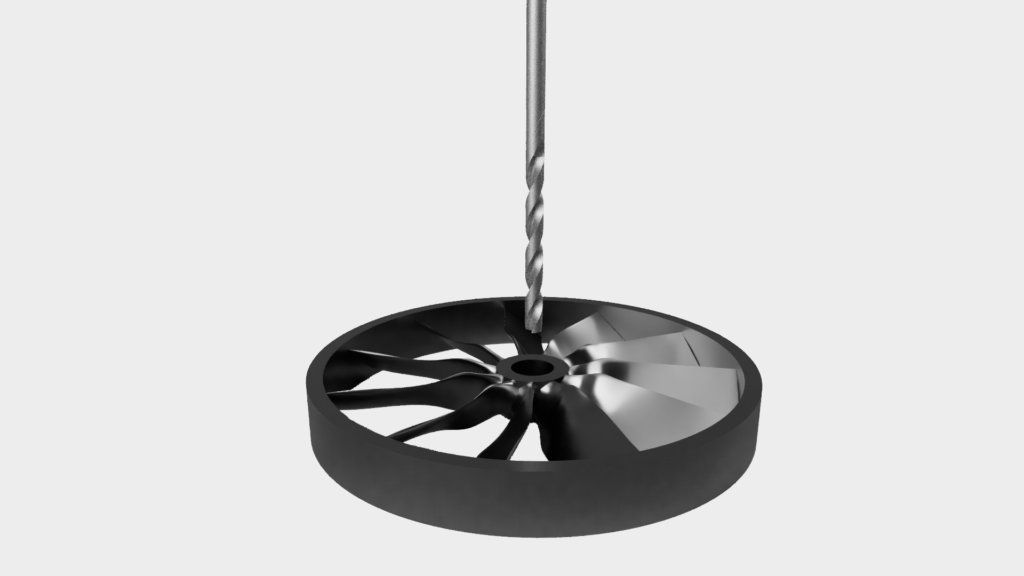
Surface refinement
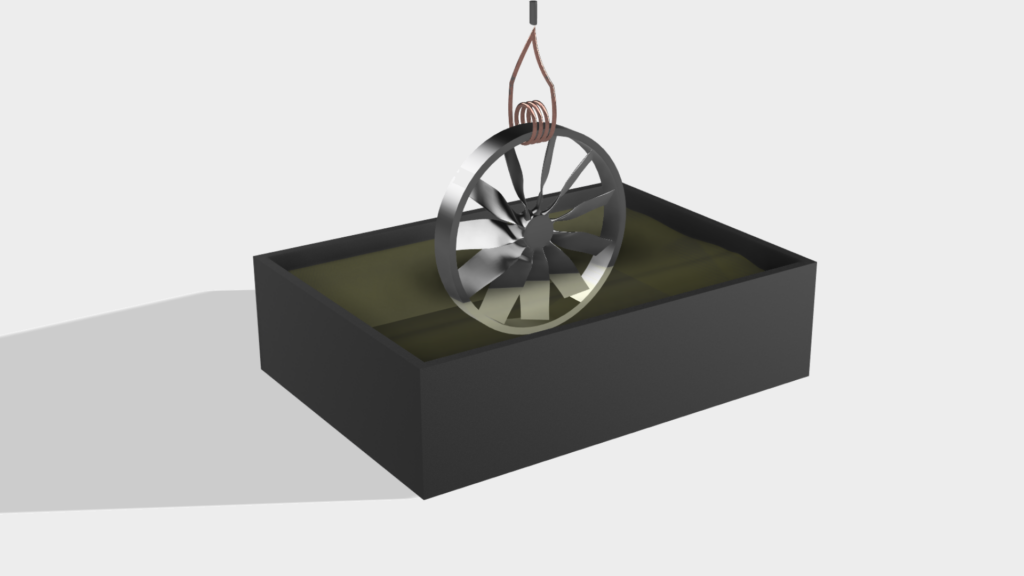
Heat treatment
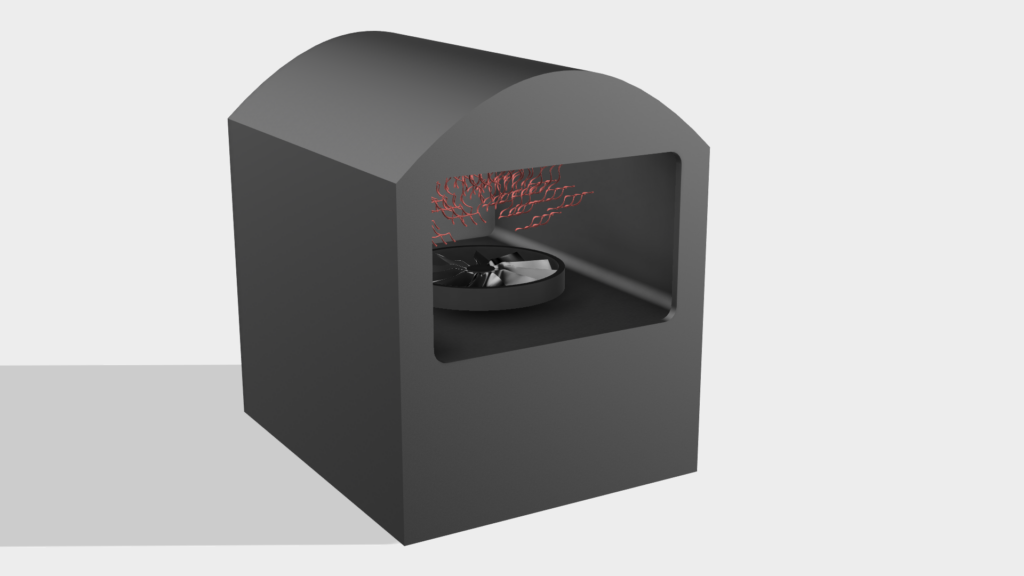
6. Quality control
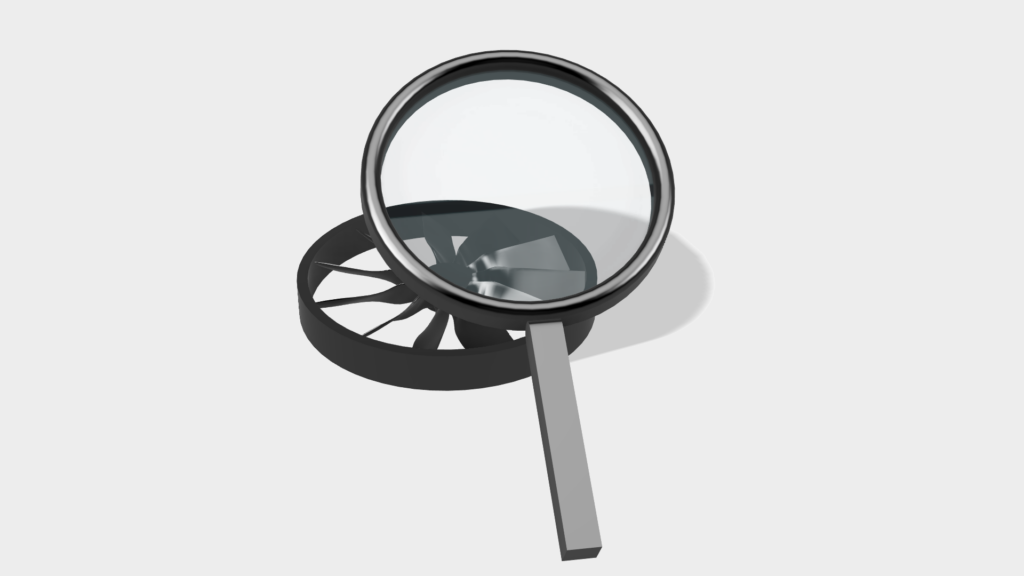
In the final step, the component is subjected to a quality check. It is carefully checked for damage or defects so that all components meet our high quality requirements. This step completes the entire process and the component is ready for use.