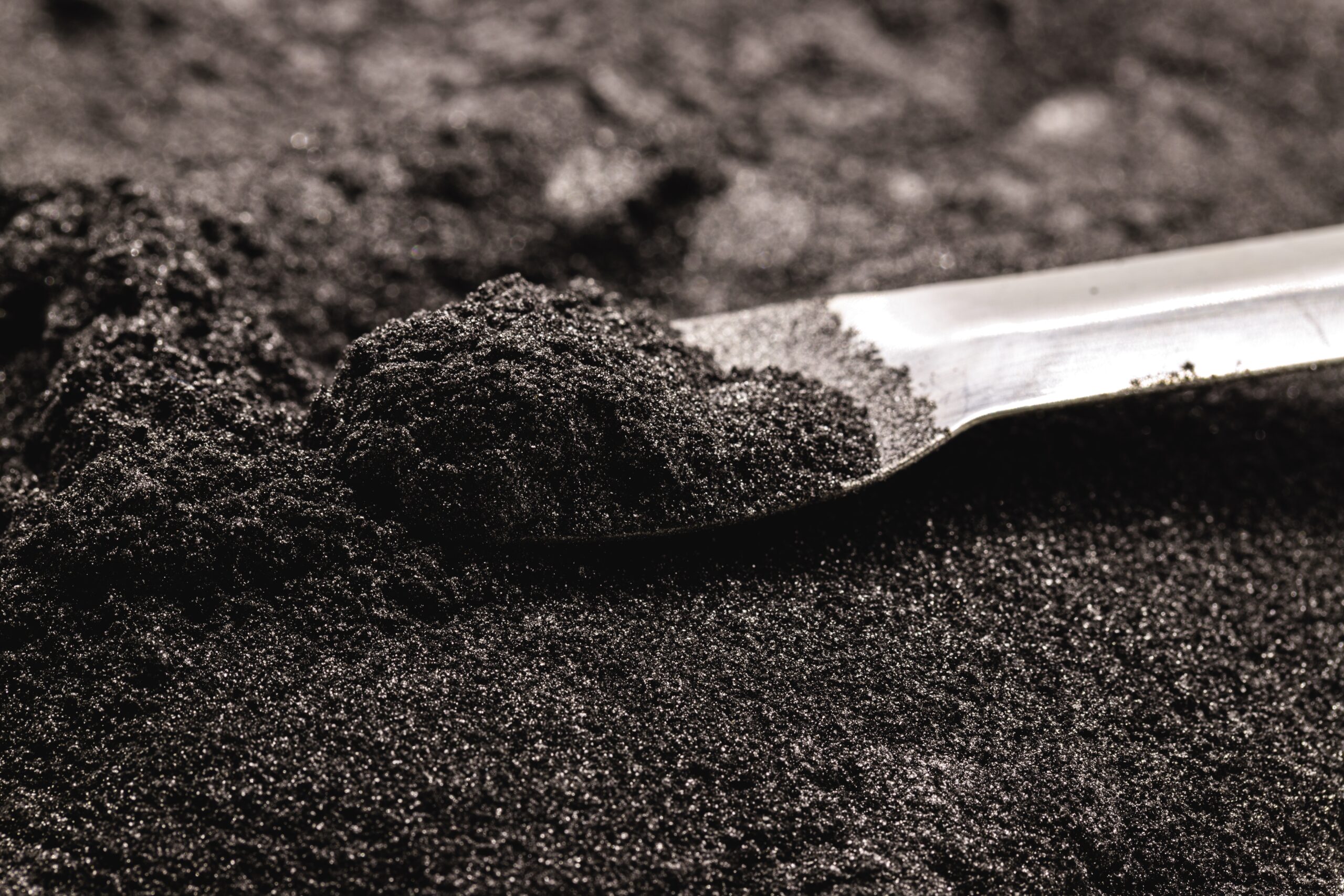
Powder Metallurgy
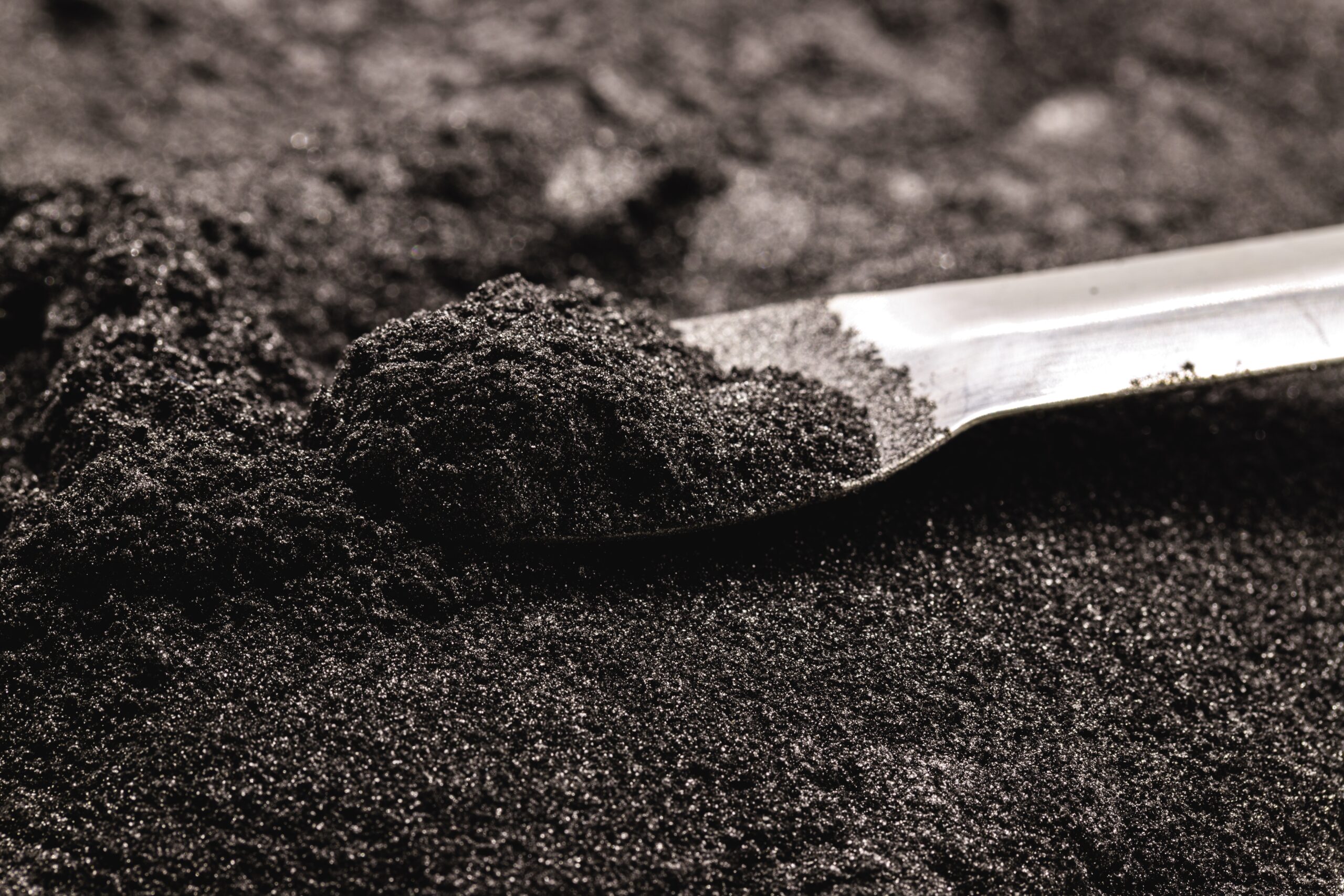
Powder Metallurgy
Powder Metallurgy
Powder metallurgy is a near-net-shape manufacturing process and is therefore particularly suitable for components with complex geometries, whereby the complexity is limited by undercuts.
The basic process steps are the production of the powder, the pressing of the component to be sintered into a green compact and the sintering process itself. The main advantages of the process are the practically rework-free production, which results in very low raw material losses, as well as the possibility of alloying “immiscible” materials.
Available materials
- Hard metals or hard materials
- Sintered iron and sintered steel
- Sintered aluminum, aluminum silicon powder
- sintered bronzes
- Other sintered materials
Powder Metallurgy
Powder metallurgy is a near-net-shape manufacturing process and is therefore particularly suitable for components with complex geometries, whereby the complexity is limited by undercuts.
The basic process steps are the production of the powder, the pressing of the component to be sintered into a green compact and the sintering process itself. The main advantages of the process are the practically rework-free production, which results in very low raw material losses, as well as the possibility of alloying “immiscible” materials.
Available materials
- Hard metals or hard materials
- Sintered iron and sintered steel
- Sintered aluminum, aluminum silicon powder
- sintered bronzes
- Other sintered materials
1. Produce powder
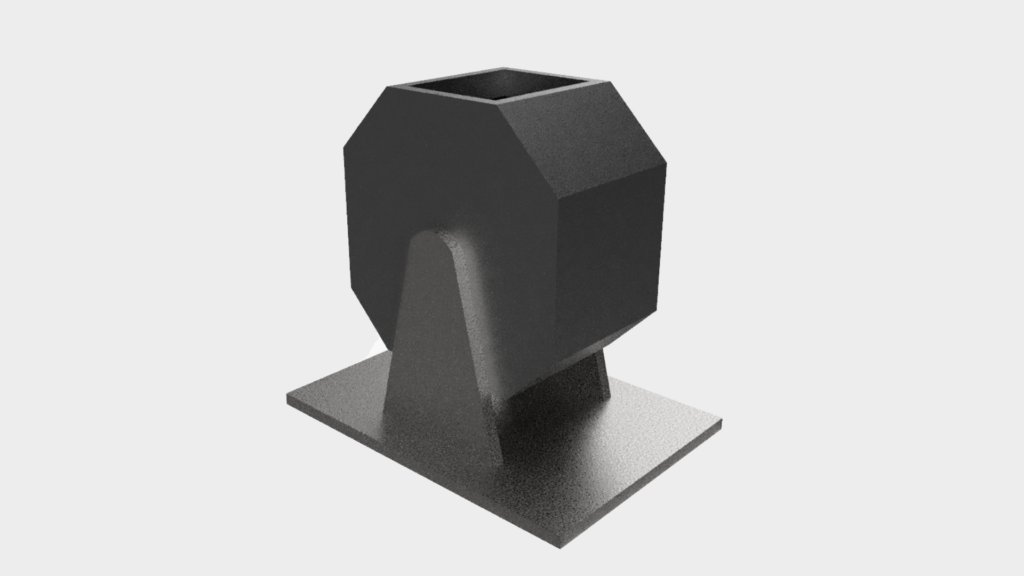
The first step is to produce the powder. To do this, metal powder and a binding agent are combined in a drum and mixed homogeneously. This ensures that the material of the component is uniform and has no defects.
2. Pressing a greenling
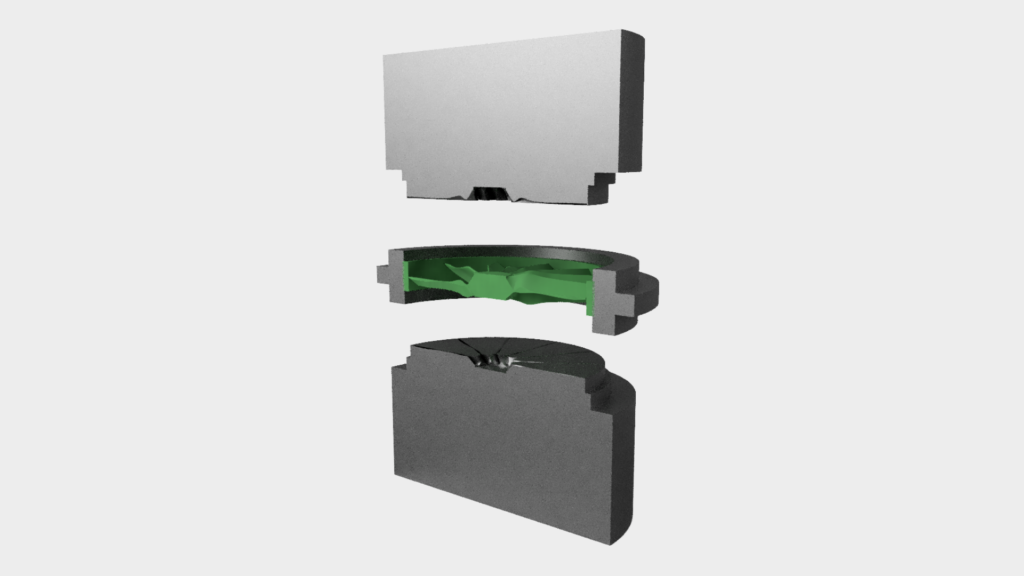
Once the material has been homogenized, the powder is pressed into a green compact. The powder is placed in a mold and compacted. At the same time, the green compact remains fragile and can easily be destroyed by hand.
3. Sintering process
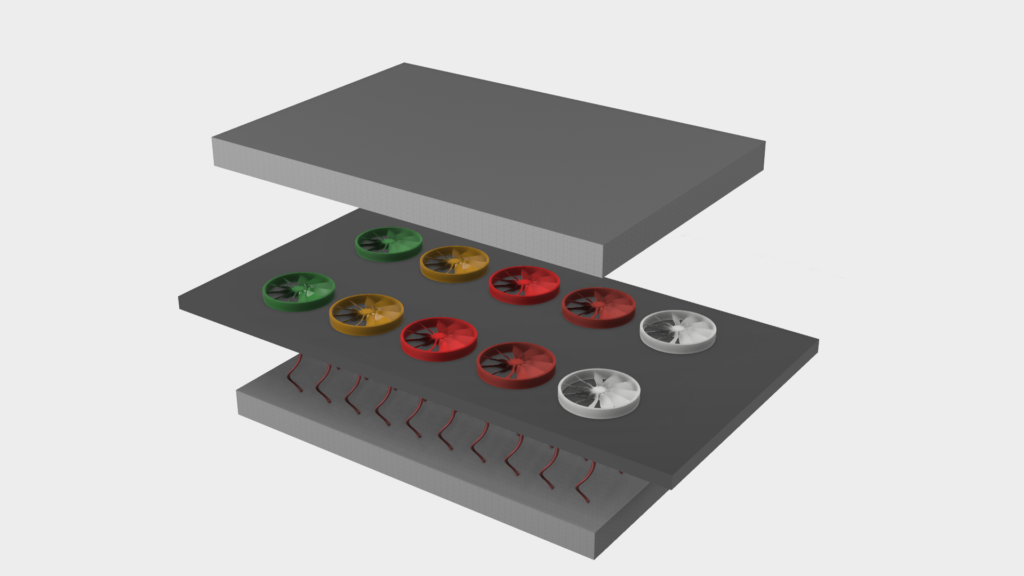
As it passes through the furnace, the binder is removed from the green compact and the remaining powder is sintered. The powder grains bond together and a solid body is formed.
4. Re-compaction
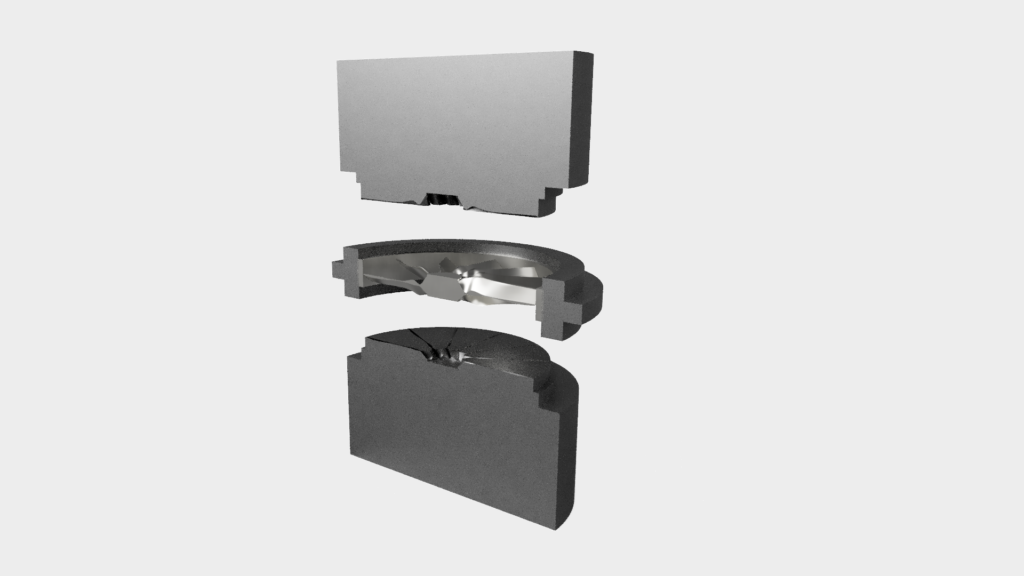
After passing through the oven, the component is compacted again, if necessary, in order to achieve the final density and thus the desired material properties.
5. Mechanical pre-machining
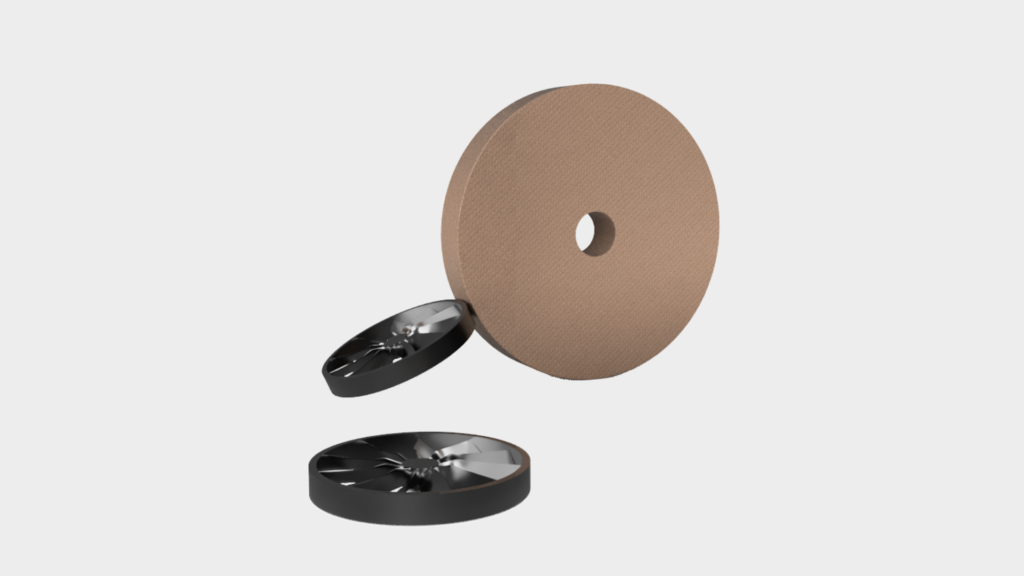
First, the components are sawn off at the original connection point. As the surface still has sprue residues, these must be removed using suitable methods such as grinding or turning.
6. Finishing
Depending on customer requirements, further processing steps can now be carried out. For example, holes and threads can be drilled, the surface galvanized or heat treated. In this step, the customer’s specific wishes and requirements are implemented.
Drilling, milling, lathing
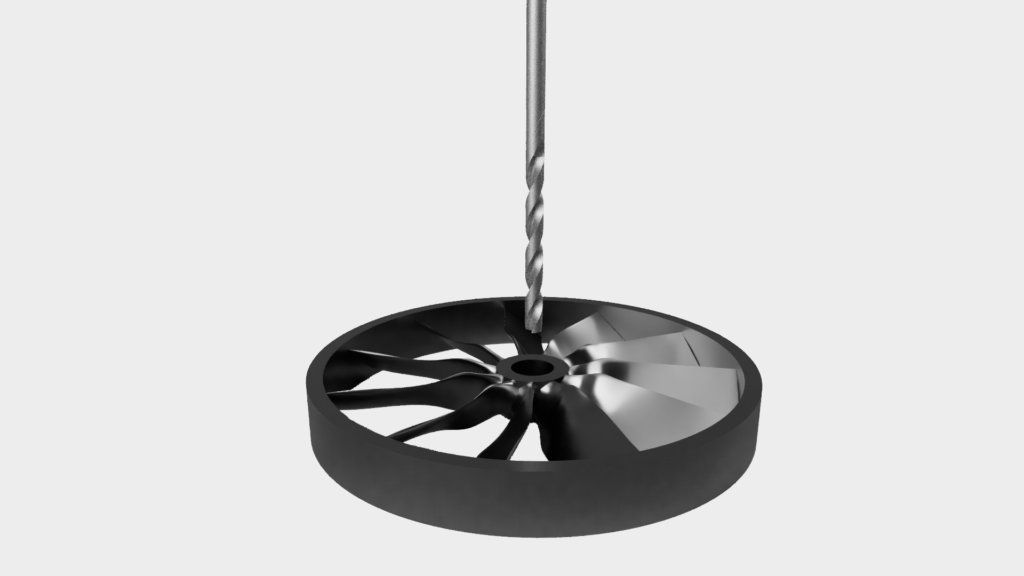
Surface refinement
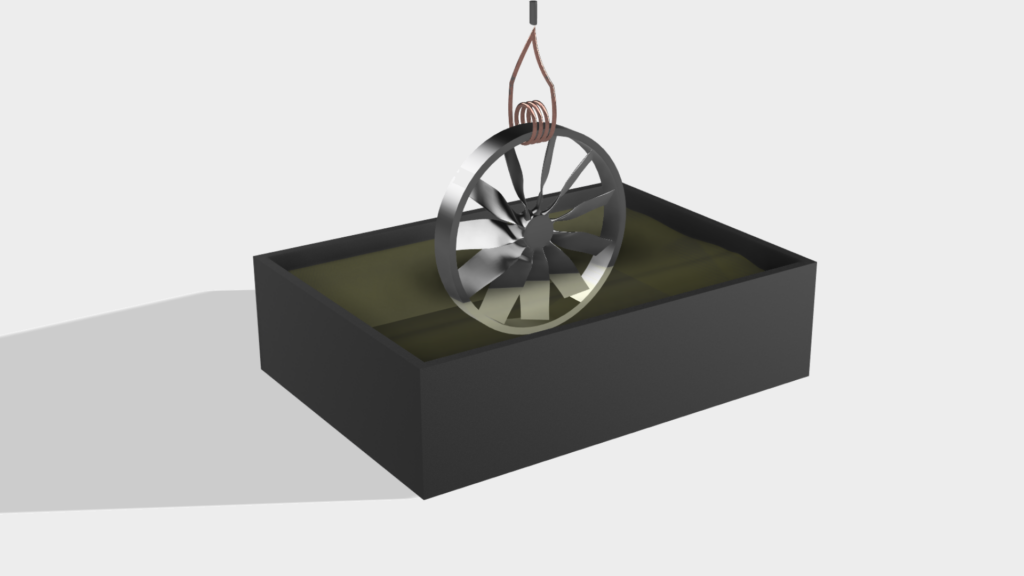
Heat treatment
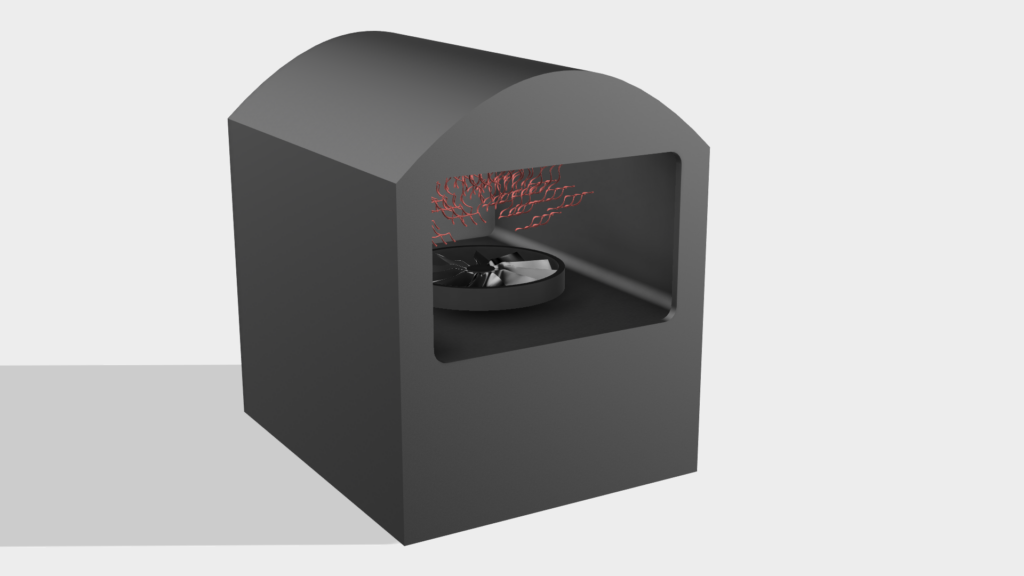
7. Quality control
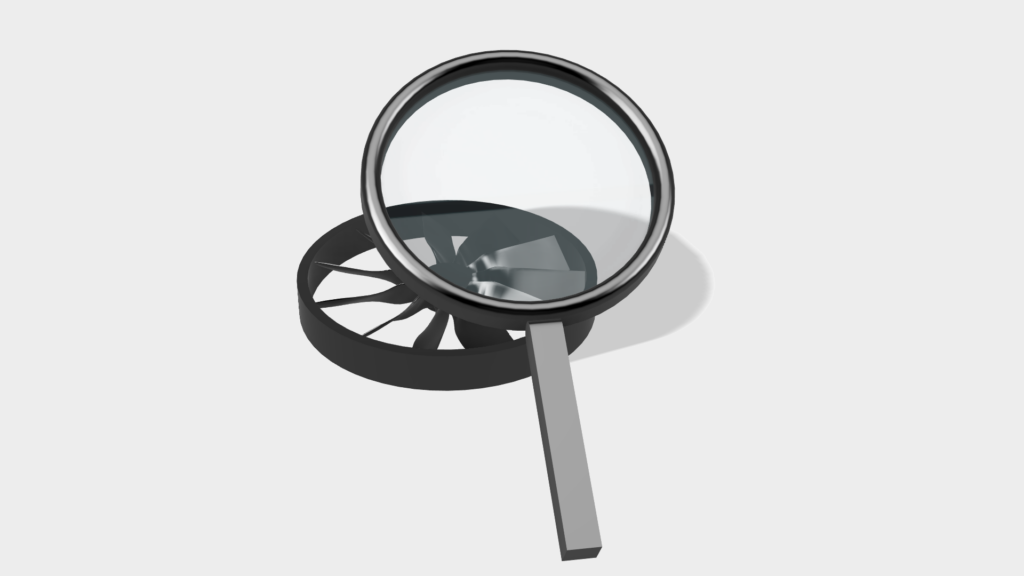
In the final step, the component is subjected to a quality check. It is carefully checked for damage or defects so that all components meet our high quality requirements. This step completes the entire process and the component is ready for use.
1. Produce powder
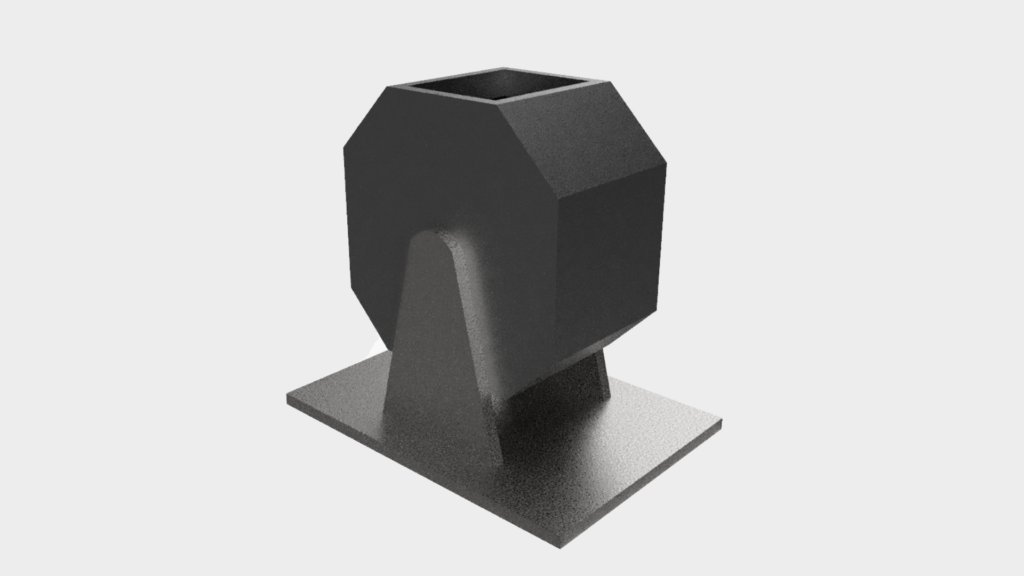
The first step is to produce the powder. To do this, metal powder and a binding agent are combined in a drum and mixed homogeneously. This ensures that the material of the component is uniform and has no defects.
2. Pressing a greenling
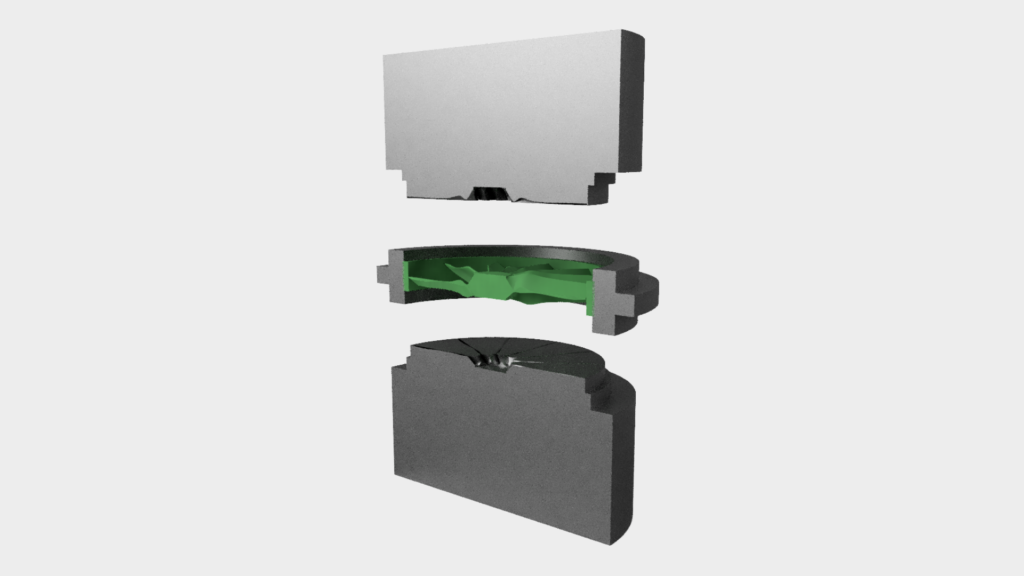
Once the material has been homogenized, the powder is pressed into a green compact. The powder is placed in a mold and compacted. At the same time, the green compact remains fragile and can easily be destroyed by hand.
3. Sintering process
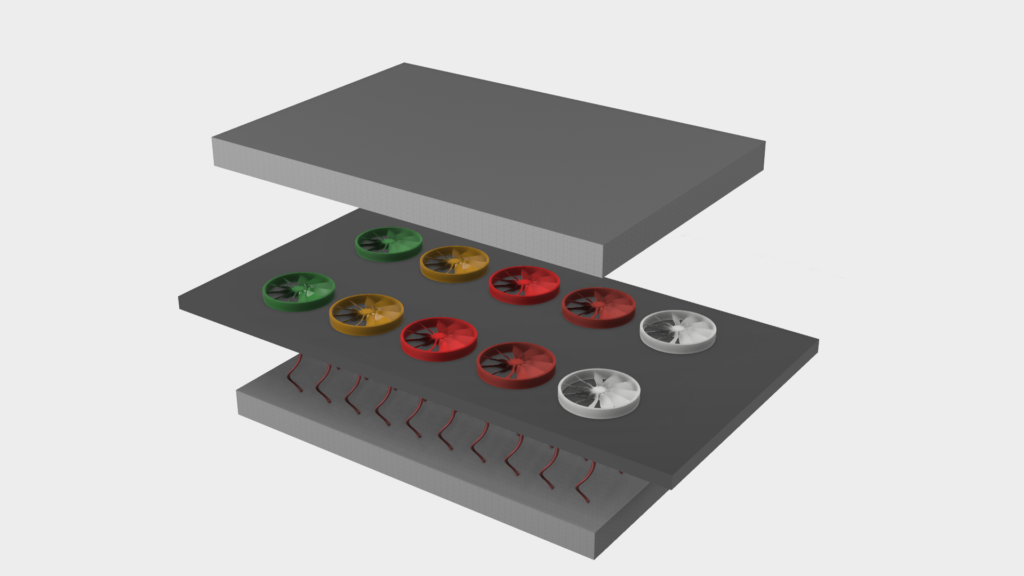
As it passes through the furnace, the binder is removed from the green compact and the remaining powder is sintered. The powder grains bond together and a solid body is formed.
4. Re-compaction
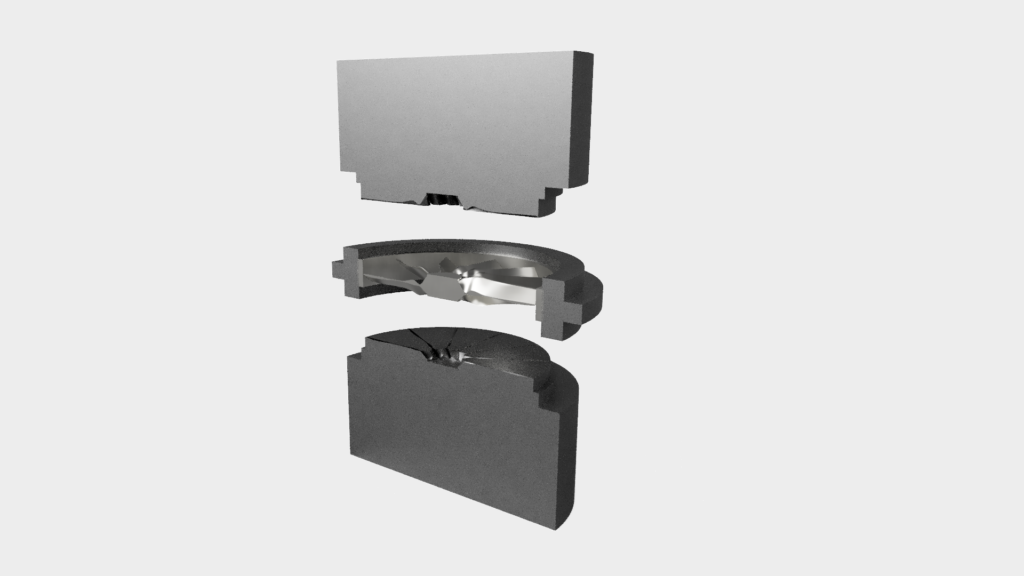
After passing through the oven, the component is compacted again, if necessary, in order to achieve the final density and thus the desired material properties.
5. Mechanical pre-machining
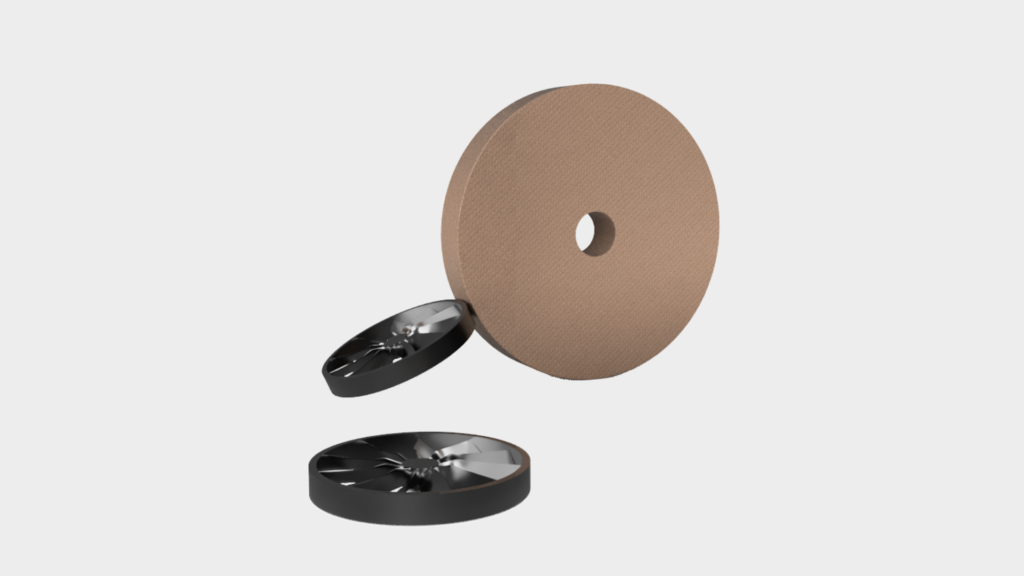
First, the components are sawn off at the original connection point. As the surface still has sprue residues, these must be removed using suitable methods such as grinding or turning.
6. Finishing
Depending on customer requirements, further processing steps can now be carried out. For example, holes and threads can be drilled, the surface galvanized or heat treated. In this step, the customer’s specific wishes and requirements are implemented.
Drilling, milling, lathing
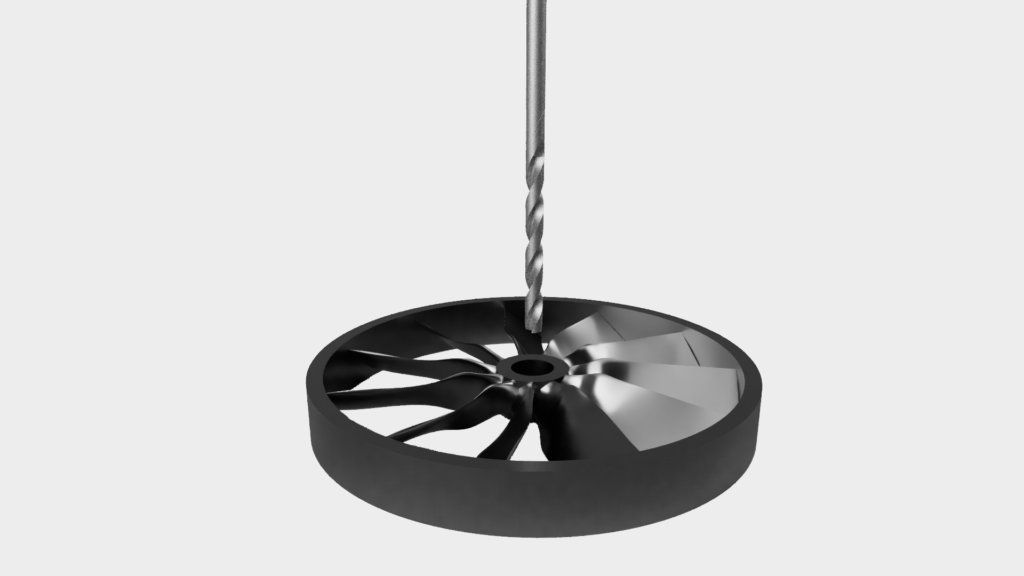
Surface refinement
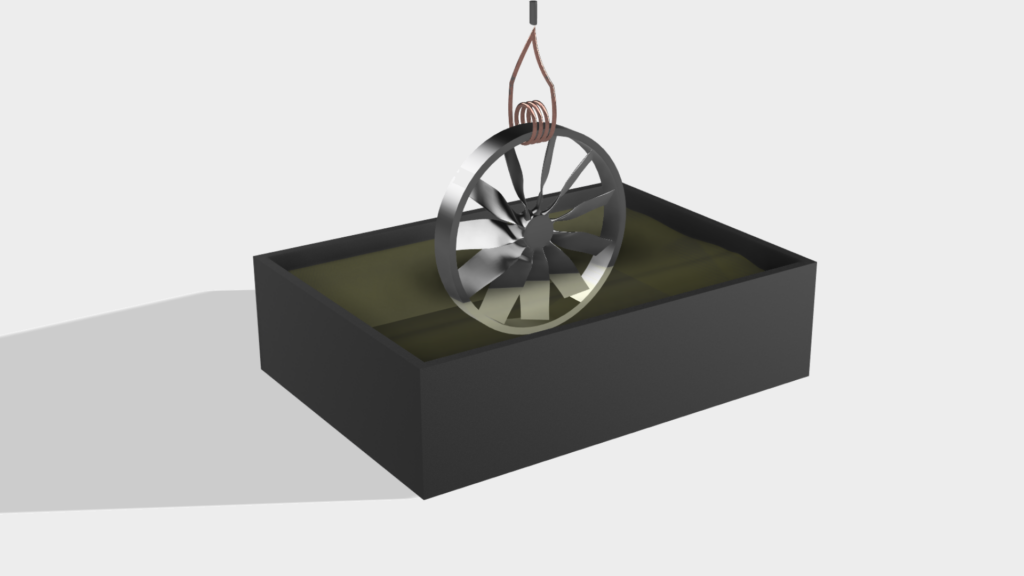
Heat treatment
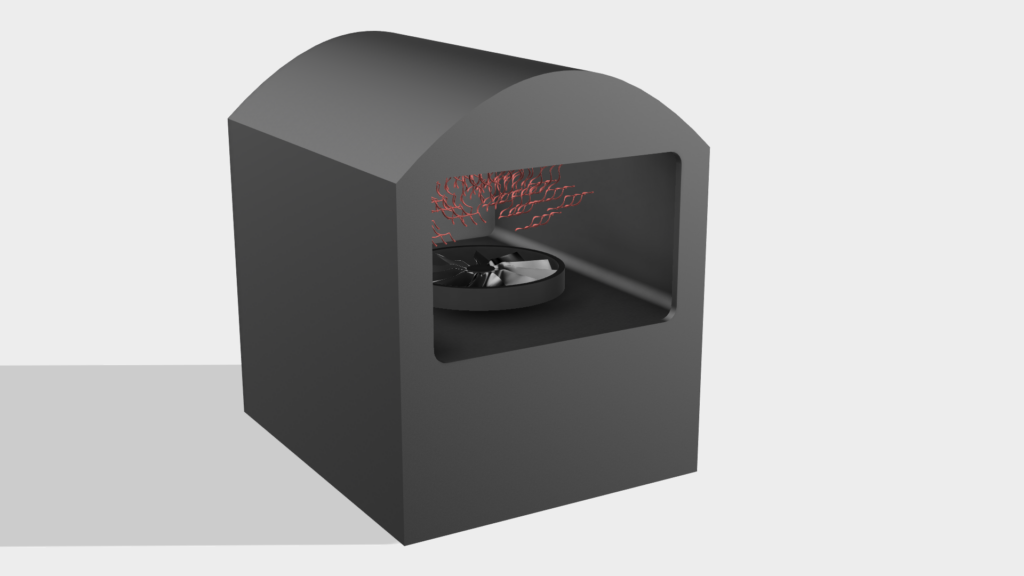
7. Quality control
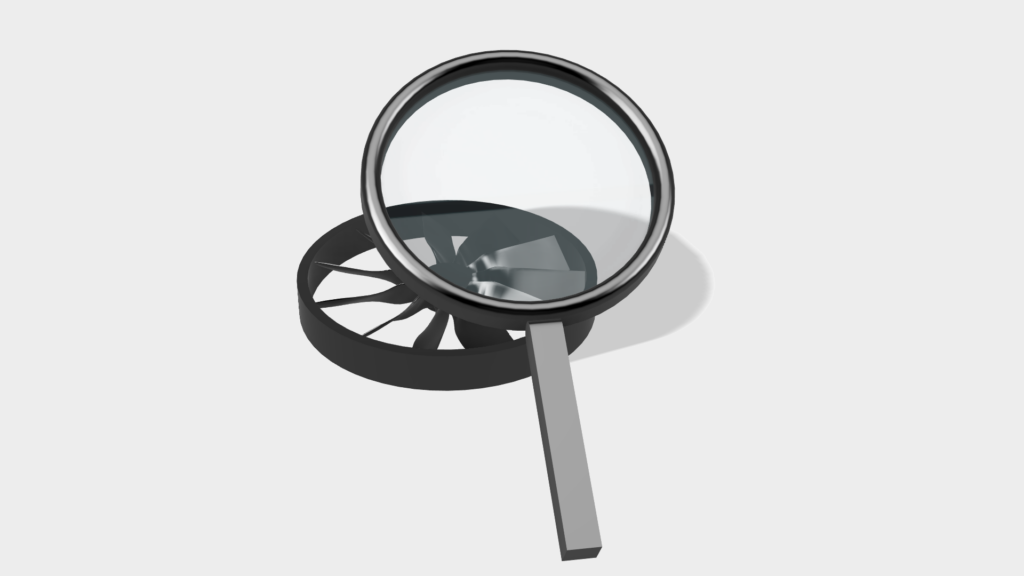
In the final step, the component is subjected to a quality check. It is carefully checked for damage or defects so that all components meet our high quality requirements. This step completes the entire process and the component is ready for use.